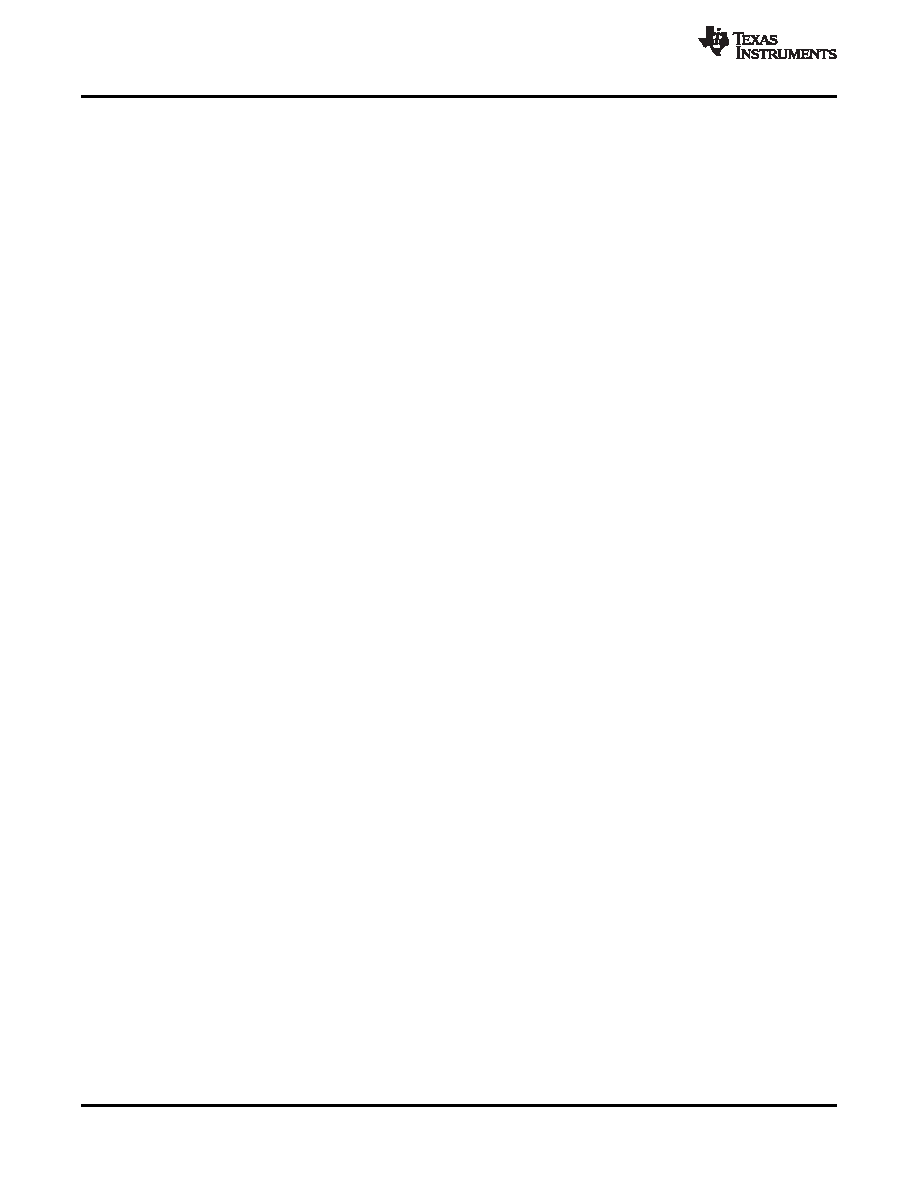
SLUSA41A
– JUNE 2010 – REVISED MARCH 2011
When the load is increased, the inductor current is always positive and the zero-crossing comparator does not
send a zero-crossing signal. The converter enters into continuous conduction mode (CCM) when no
zero-crossing is detected for two consecutive PWM pulses. The switching synchronizes to the internal clock and
the switching frequency is fixed.
In high-efficiency mode (HEF), the operation is the same as diode emulation mode at light load. However, the
converter does not synchronize to the internal clock during CCM. Instead, the PWM modulator determines the
switching frequency.
LIGHT LOAD OPERATION
In skip modes (DE and HEF) when the load current is less than one-half of the inductor peak current, the
inductor current becomes negative by the end of off-time. During light load operation, the low-side MOSFET is
turned off when the inductor current reaches zero. The energy delivered to the load per switching cycle is
increased compared to the normal PWM mode operation and the switching frequency is reduced. The switching
loss is reduced, thereby improving efficiency.
In both DE and HEF mode, the switching frequency is reduced in discontinuous conduction mode (DCM). When
the load current is 0 A, the minimum switching frequency is reached. The difference between VVBST and VSW
must be maintained at a value higher than 2.4 V.
FORCED CONTINUOUS CONDUCTION MODE
When the PS pin is grounded or greater than 2.2 V, the TPS53311 is operating in forced continuous conduction
mode in both light-load and heavy-load conditions. In this mode, the switching frequency remains constant over
the entire load range, making it suitable for applications that need tight control of switching frequency at a cost of
lower efficiency at light load.
SOFT START
The soft-start function reduces the inrush current during the start up sequence. A slow-rising reference voltage is
generated by the soft-start circuitry and sent to the input of the error amplifier. When the soft-start ramp voltage
is less than 600 mV, the error amplifier uses this ramp voltage as the reference. When the ramp voltage reaches
600 mV, the error amplifier switches to a fixed 600-mV reference. The typical soft-start time is 400
s.
POWER GOOD
The TPS53311 monitors the voltage on the FB pin. If the FB voltage is between 83% and 117% of the reference
voltage, the power good signal remains high. If the FB voltage falls outside of these limits, the internal open drain
output pulls the power good pin (PGD) low.
During start-up, the input voltage must be higher than 1 V in order to have valid power good logic, and the power
good signal is delayed for 400
s after the FB voltage falls to within the power good limits. There is also 10-s
delay during the shut down sequence.
UNDERVOLTAGE LOCKOUT (UVLO) FUNCTION
The TPS53311 provides undervoltage lockout (UVLO) protection for both power input (VIN) and bias input (VDD)
voltage. If either of them is lower than the UVLO threshold voltage minus the hysteresis, the device shuts off.
When the voltage rises above the threshold voltage, the device restarts. The typical UVLO rising threshold is 2.8
V for both VIN and VVDD. A hysteresis voltage of 130 mV for VIN and 75 mV for VVDD is also provided to prevent
glitch.
OVERCURRENT PROTECTION
The TPS53311 continuously monitors the current flowing through the high-side and the low-side MOSFETs. If
the current through the high-side FET exceeds 4.5 A, the high-side FET turns off and the low-side FET turns on
until the next PWM cycle. An overcurrent (OC) counter starts to increment each occurrence of an overcurrent
event. The converter shuts down immediately when the OC counter reaches four. The OC counter resets if the
detected current is less 4.5 A after an OC event.
12
Copyright
2010–2011, Texas Instruments Incorporated