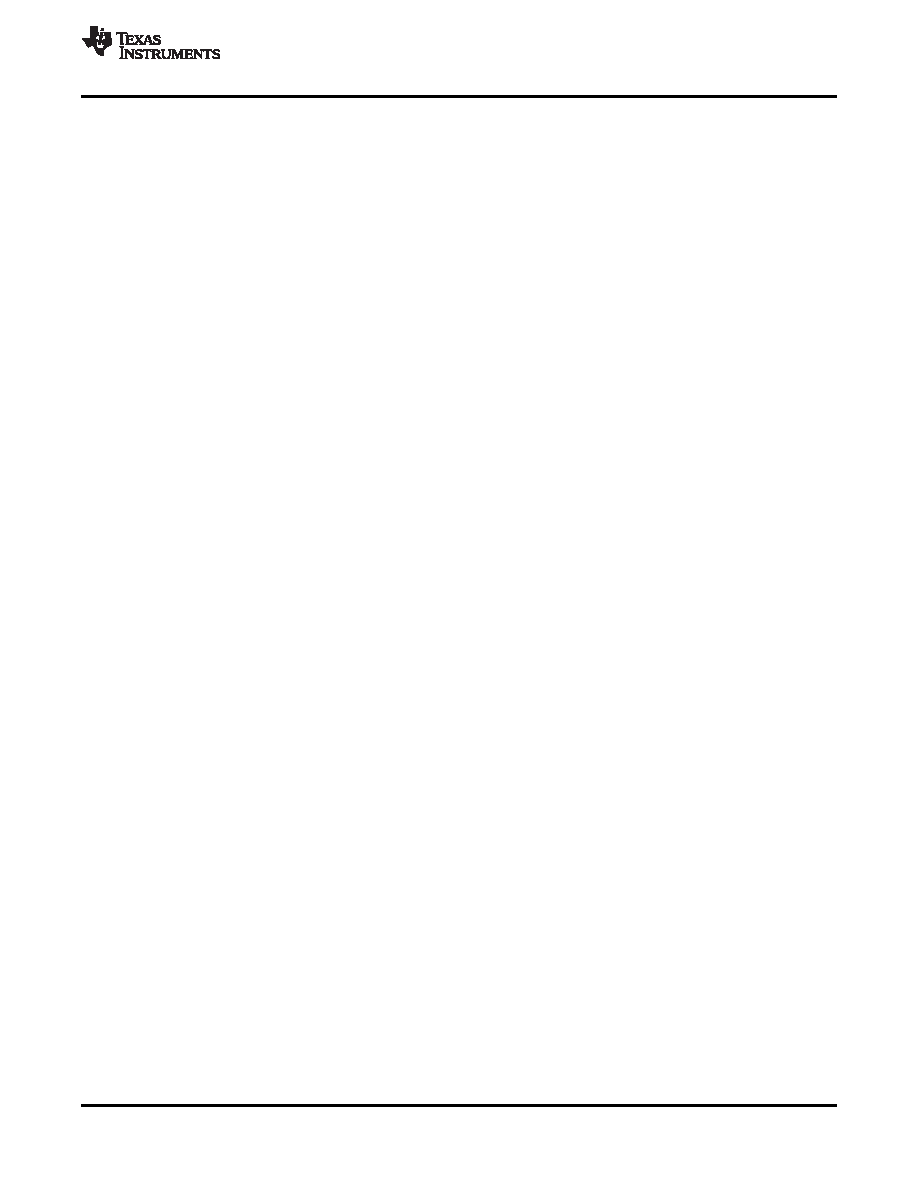
SLUSA41A
– JUNE 2010 – REVISED MARCH 2011
Another set of overcurrent circuitry monitors the current flowing through low-side FET. If the current through the
low-side FET exceeds 5.1 A, the overcurrent protection is enabled and immediately turns off both the high-side
and the low-side FETs and shuts down the converter. The device is fully protected against overcurrent during
both on-time and off-time. This protection is latched. Please refer to the TPS53310 data sheet
(SLUSA68) for
information on hiccup overcurrent protection.
OVERVOLTAGE PROTECTION
The TPS53311 monitors the voltage divided feedback voltage to detect overvoltage and undervoltage conditions.
When the feedback voltage is greater than 117% of the reference, the high-side MOSFET turns off and the
low-side MOSFET turns on. The output voltage then drops until it reaches the undervoltage threshold. At that
point the low-side MOSFET turns off and the device enters a high-impedance state.
UNDERVOLTAGE PROTECTION
When the feedback voltage is lower than 83% of the reference voltage, the undervoltage protection timer starts.
If the feedback voltage remains lower than the undervoltage threshold voltage after 10
μs, the device turns off
both the high-side and the low-side MOSFETs and goes into a high-impedance state. This protection is latched.
OVERTEMPERATURE PROTECTION
The TPS53311 continuously monitors the die temperature. If the die temperature exceeds the threshold value
(140
C typical), the device shuts off. When the device temperature falls to 40C below the overtemperature
threshold, it restarts and returns to normal operation.
OUTPUT DISCHARGE
When the enable pin is low, the TPS53311 discharges the output capacitors through an internal MOSFET switch
between SW and PGND while high-side and low-side MOSFETs remain off. The typical discharge switch-on
resistance is 60
Ω. This function is disabled when VIN is less than 1 V.
MASTER/SLAVE OPERATION AND SYNCHRONIZATION
Two TPS53311 can operate interleaved when configured as master/slave. The SYNC pins of the two devices are
connected together for synchronization. In CCM, the master device sends the 180
° out-of-phase pulse to the
slave device through the SYNC pin, which determines the leading edge of the PWM pulse. If the slave device
does not receive the SYNC pulse from the master device or if the SYNC connection is broken during operation,
the slave device continues to operate using its own internal clock.
In DE mode, the master/slave switching node does not synchronize to each other if either one of them is
operating in DCM. When both master and slave enters CCM, the switching nodes of master and slave
synchronize to each other.
The SYNC pin of the slave device can also connect to external clock source within
±20% of the 1.1-MHz
switching frequency. The falling edge of the SYNC triggers the rising edge of the PWM signal.
Copyright
2010–2011, Texas Instruments Incorporated
13