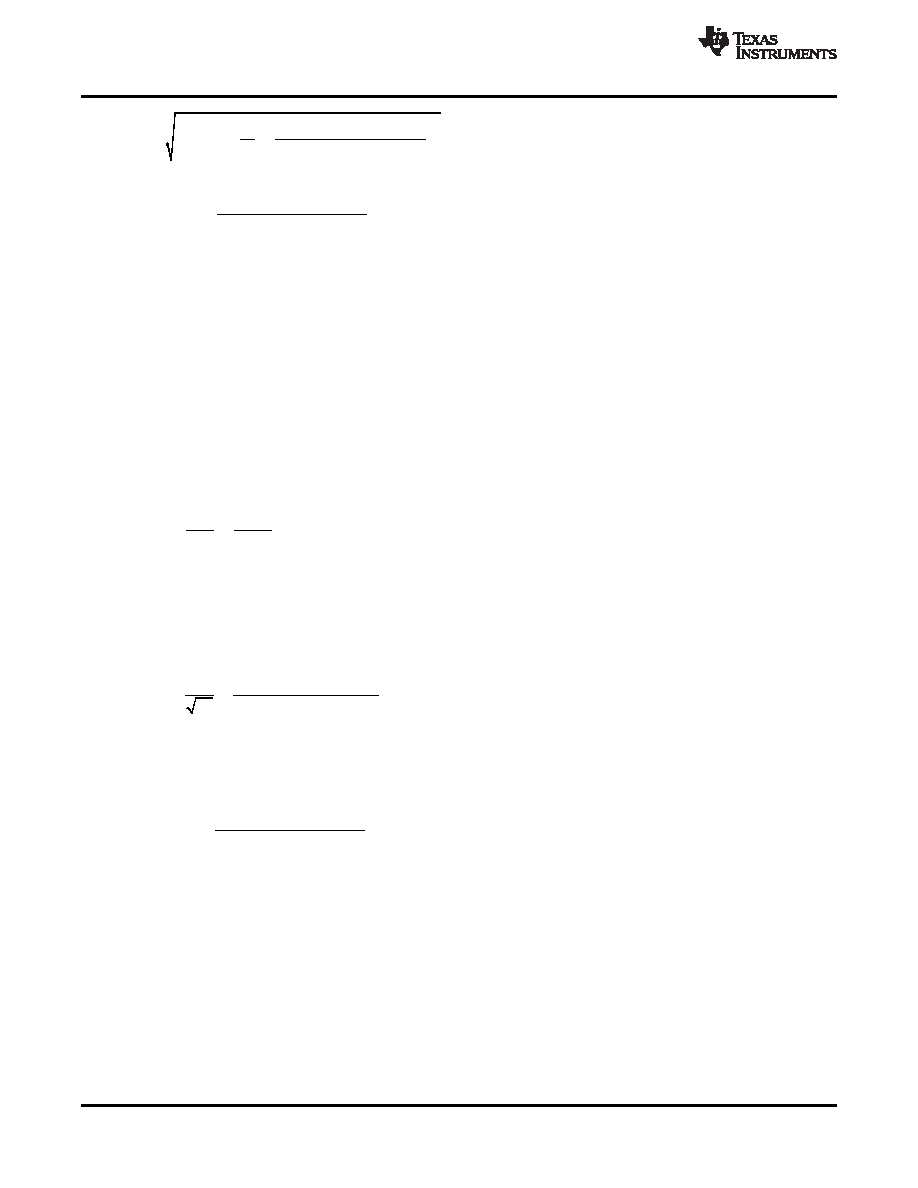
(
)
2
1
12
2
OUT
IN(MAX)
OUT
L(RMS)
OUT(MAX)
IN(MAX)
OUT
SW
V
I
V
L
F
0.8
-
=
+
÷
è
OUT
IN(MAX)
OUT
L(PK)
OUT(MAX)
OUT
IN(MAX)
SW
V
(V
-V
)
I
1.6
V
L
F
=
+
OUT MIN
OUT
CO
K
C
L
2
(
)
1
=
÷
2p
è
)
OUT
IN(MAX)
OUT
COUT(RMS)
IN(MAX)
OUT
SW
C
1
V
(V
V
I
V
L
F
N
12
-
é
ù
=
ê
ú
(
)
D
÷
÷
è
IN(MAX)
OUT
SW
MAX
C
p-p(MAX)
OUT
IN(MAX)
OUT
V
L
F
0.8
ESR
=N
V
-V
SLVS500C
– DECEMBER 2003 – REVISED FEBRUARY 2011
(5)
The peak inductor current is determined from
Equation 6:(6)
For this design, the RMS inductor current is 1.503 A and the peak inductor current is 1.673 A. The inductor
chosen is a Coilcraft DS3316P-682 6.8
H. It has a saturationcurrent rating of 2.8 A and an RMS current rating
of 2.2 A, easily meeting these requirements.
Capacitor Selection
The important design parameters for the output capacitor are dc voltage, ripple current, and equivalent series
resistance (ESR). The dc-voltage and ripple-current ratings must not be exceeded. The ESR rating is important
because along with the inductor current it determines the output ripple voltage level. The actual value of the
output capacitor is not critical, but some practical limits do exist. Consider the relationship between the desired
closed-loop crossover frequency of the design and LC corner frequency of the output filter. In general, it is
desirable to keep the closed-loop crossover frequency at less than 1/5 of the switching frequency. With high
switching frequencies such as the 700 kHz frequency of this design, internal circuit limitations of the TPS54110
limit the practical maximum crossover frequency to about 100 kHz. To allow adequate phase gain in the
compensation network, set the LC corner frequency to approximately one decade below the closed-loop
crossover frequency. This limits the minimum capacitor value for the output filter to:
(7)
where K is the frequency multiplier for the spread between fLC and fCO. K should be between 5 and 15, typically
10 for one decade of difference.
For a desired crossover of 60 kHz, K=10 and a 6.8
μH inductor, the minimum value for the output capacitor is
100
μF. The selected output capacitor must be rated for a voltage greater than the desired output voltage plus
one half the ripple voltage. Any derating factors must also be included. The maximum RMS ripple current in the
(8)
where NC is the number of output capacitors in parallel.
The maximum ESR of the output capacitor is determined by the allowable output ripple specified in the initial
design parameters. The output ripple voltage is the inductor ripple current times the ESR of the output filter so
the maximum specified ESR as listed in the capacitor data sheet is given by
Equation 9:(9)
For this design example, a single 100
F output capacitor is chosen for C2. The calculated RMS ripple current is
80 mA and the maximum ESR required is 87 m
Ω. An example of a suitable capacitor is the Sanyo Poscap
6TPC100M, rated at 6.3 V with a maximum ESR of 45 milliohms and a ripple-current rating of 1.7 A.
Other capacitor types work well with the TPS54110, depending on the needs of the application.
Compensation Components
The external compensation used with the TPS54110 allows for a wide range of output-filter configurations. A
large range of capacitor values and dielectric types are supported. The design example uses type 3
compensation consisting of R1, R3, R5, C6, C7 and C8. Additionally, R2 and R1 form a voltage-divider network
that sets the output voltage. These component reference designators are the same as those used in the SWIFT
Designer Software.
10
2003–2011, Texas Instruments Incorporated