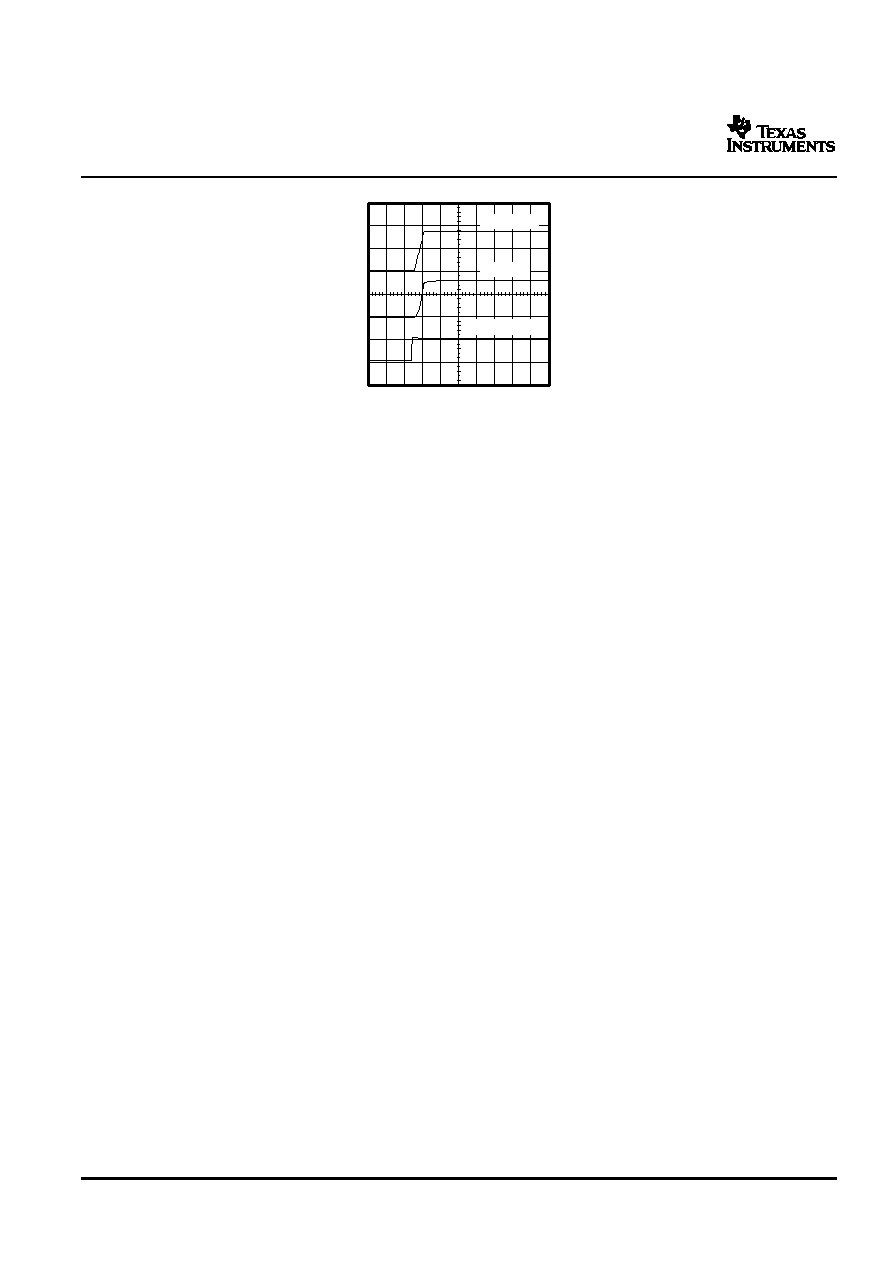
www.ti.com
V
(2 V/Div)
O
I (2 A/Div)
I
Q1Vds (5 V/Div)
t - Time = 10 msec/Div
REMOTE SENSE
Auto-Track FUNCTION
PTH04040W
SLTS238A – SEPTEMBER 2005 – REVISED FEBRUARY 2006
Figure 14. Power-Up from Inhibit Control
The remote sense feature allows the regulator to compensate for limited amounts of voltage drop, that may be
incurred between the converter and load, due to resistance in the PCB traces. Connecting the +Sense and
–Sense pins to the respective VO and GND output nodes improves the load regulation of the regulator output at
those connection points. This is recommended even if the load circuit is located close to the module.
If either the +Sense and –Sense are left open-circuit, an internal low-value resistor (15-
or less), connected
from the respective sense pin to either VO or GND, ensures the output voltage remains in regulation.
With the sense pins connected, the difference between the voltage measured across the VO and GND pins of the
regulator, and that measured at +Sense with respect to +Sense, is the amount of IR drop being compensated by
the regulator. This should be limited to a maximum of 0.3 V.
Note: The remote sense feature is not designed to compensate for the forward drop of nonlinear or
frequency dependent components that may be placed in series with the converter output. Examples include
OR-ing diodes, filter inductors, ferrite beads, and fuses. When these components are enclosed by the remote
sense connection they are effectively placed inside the regulation control loop, which can adversely affect the
stability of the regulator.
The Auto-Track function is unique to the PTH/PTV family, and is available with the all POLA-compatible
products. Auto-Track was designed to simplify the amount of circuitry required to make the output voltage from
each module power up and power down in sequence. The sequencing of two or more supply voltages during
power up is a common requirement for complex mixed-signal applications, that use dual-voltage VLSI ICs such
as the TMS320 DSP family, micro-processors, and ASICs.
HOW Auto-Track WORKS
Auto-Track works by forcing the module’s output voltage to follow a voltage presented at the Track control pin.
This control range is limited to between 0 V and the module’s set-point voltage. Once the Track input is raised
above the set-point voltage, the module’s output remains at its set-point 1. As an example, if the Track pin of a
2.5-V regulator is at 1 V, the regulated output will be 1 V. But, if the voltage at the Track pin rises to 3 V, the
regulated output does not go higher than 2.5 V.
When the Track input is used to connect a number of modules together, it forces the output voltage from each
module to follow a common signal during power-up and power-down. The control signal can be an externally
generated master ramp waveform, or the output voltage from another power supply circuit.(3) For convenience,
each module’s Track input incorporates an internal RC charge circuit. This operates off the module’s input
voltage to provide a suitable rising voltage ramp waveform.
TYPICAL APPLICATION
Connecting the Track inputs of two or more modules forces their Track input to follow the same collective RC
ramp waveform, and allows their power-up sequence to be coordinated from a common Track control signal.
This can be an open-collector (or open drain) device, such as a power-up reset voltage supervisor IC.
16
Submit Documentation Feedback