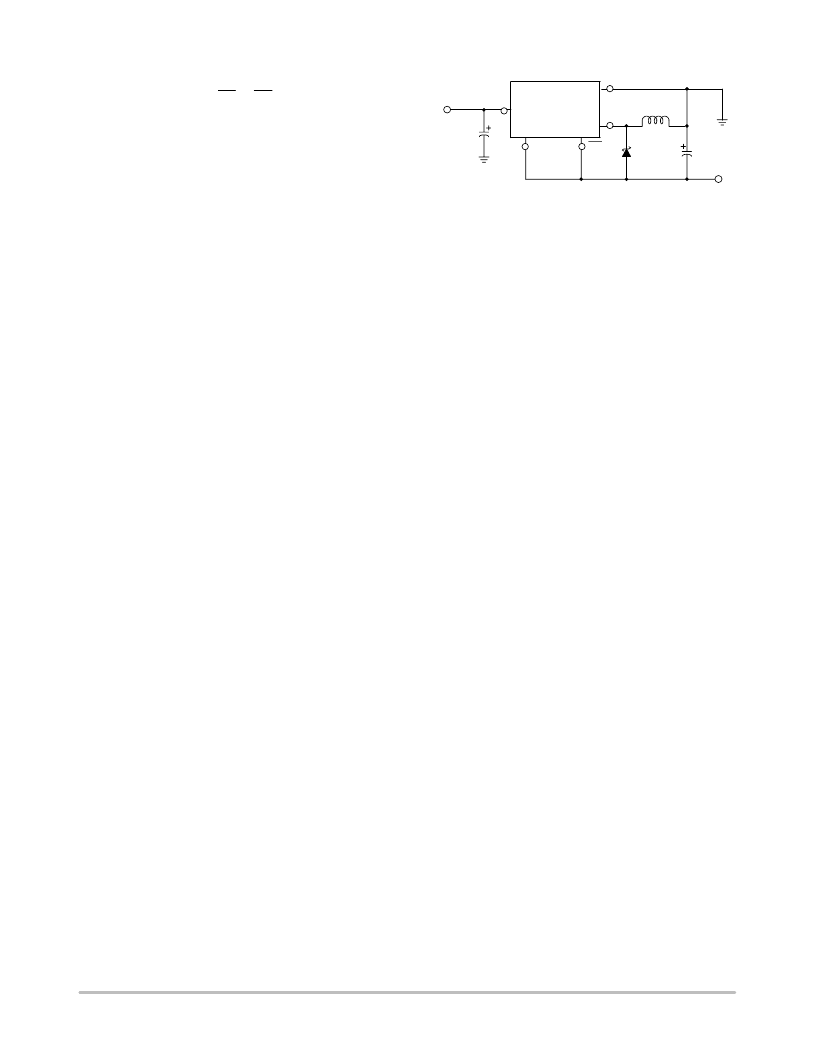
LM2575
http://onsemi.com
18
d
ton
T
VO
Vin
,
I
Q
(quiescent current) and V
sat
can be found in the
LM2575 data sheet,
is minimum input voltage applied,
is the regulator output voltage,
I
Load
is the load current.
The dynamic switching losses during turnon and
turnoff can be neglected if proper type catch diode is used.
V
in
V
O
Packages Not on a Heatsink (FreeStanding)
For a freestanding application when no heatsink is used,
the junction temperature can be determined by the following
expression:
T
J
= (R
JA
) (P
D
) + T
A
where (R
JA
)(P
D
) represents the junction temperature rise
caused by the dissipated power and T
A
is the maximum
ambient temperature.
Packages on a Heatsink
If the actual operating junction temperature is greater than
the selected safe operating junction temperature determined
in step 3, than a heatsink is required. The junction
temperature will be calculated as follows:
T
J
= P
D
(R
JA
+ R
CS
+ R
SA
) + T
A
where
R
JC
is the thermal resistance junctioncase,
R
CS
is the thermal resistance caseheatsink,
R
SA
is the thermal resistance heatsinkambient.
If the actual operating temperature is greater than the
selected safe operating junction temperature, then a larger
heatsink is required.
Some Aspects That can Influence Thermal Design
It should be noted that the package thermal resistance and
the junction temperature rise numbers are all approximate,
and there are many factors that will affect these numbers,
such as PC board size, shape, thickness, physical position,
location, board temperature, as well as whether the
surrounding air is moving or still.
Other factors are trace width, total printed circuit copper
area, copper thickness, single or doublesided, multilayer
board, the amount of solder on the board or even color of the
traces.
The size, quantity and spacing of other components on
the board can also influence its effectiveness to dissipate
the heat.
Figure 25. Inverting BuckBoost Regulator Using the
LM257512 Develops 12 V @ 0.35 A
D1
1N5819
L1
100 H
Output
2
4
Feedback
Unregulated
DC Input
12 V to 25 V
C
in
100 F
/50 V
1
5
3
ON/OFF
GND
+V
in
Regulated
Output
12 V @ 0.35 A
C
out
1800 F
/16 V
LM257512
ADDITIONAL APPLICATIONS
Inverting Regulator
An inverting buckboost regulator using the LM257512
is shown in Figure 25. This circuit converts a positive input
voltage to a negative output voltage with a common ground
by bootstrapping the regulators ground to the negative
output voltage. By grounding the feedback pin, the regulator
senses the inverted output voltage and regulates it.
In this example the LM257512 is used to generate a
12 V output. The maximum input voltage in this case
cannot exceed +28 V because the maximum voltage
appearing across the regulator is the absolute sum of the
input and output voltages and this must be limited to a
maximum of 40 V.
This circuit configuration is able to deliver approximately
0.35 A to the output when the input voltage is 12 V or higher.
At lighter loads the minimum input voltage required drops
to approximately 4.7 V, because the buckboost regulator
topology can produce an output voltage that, in its absolute
value, is either greater or less than the input voltage.
Since the switch currents in this buckboost configuration
are higher than in the standard buck converter topology, the
available output current is lower.
This type of buckboost inverting regulator can also
require a larger amount of startup input current, even for
light loads. This may overload an input power source with
a current limit less than 1.5 A.
Such an amount of input startup current is needed for at
least 2.0 ms or more. The actual time depends on the output
voltage and size of the output capacitor.
Because of the relatively high startup currents required by
this inverting regulator topology, the use of a delayed startup
or an undervoltage lockout circuit is recommended.