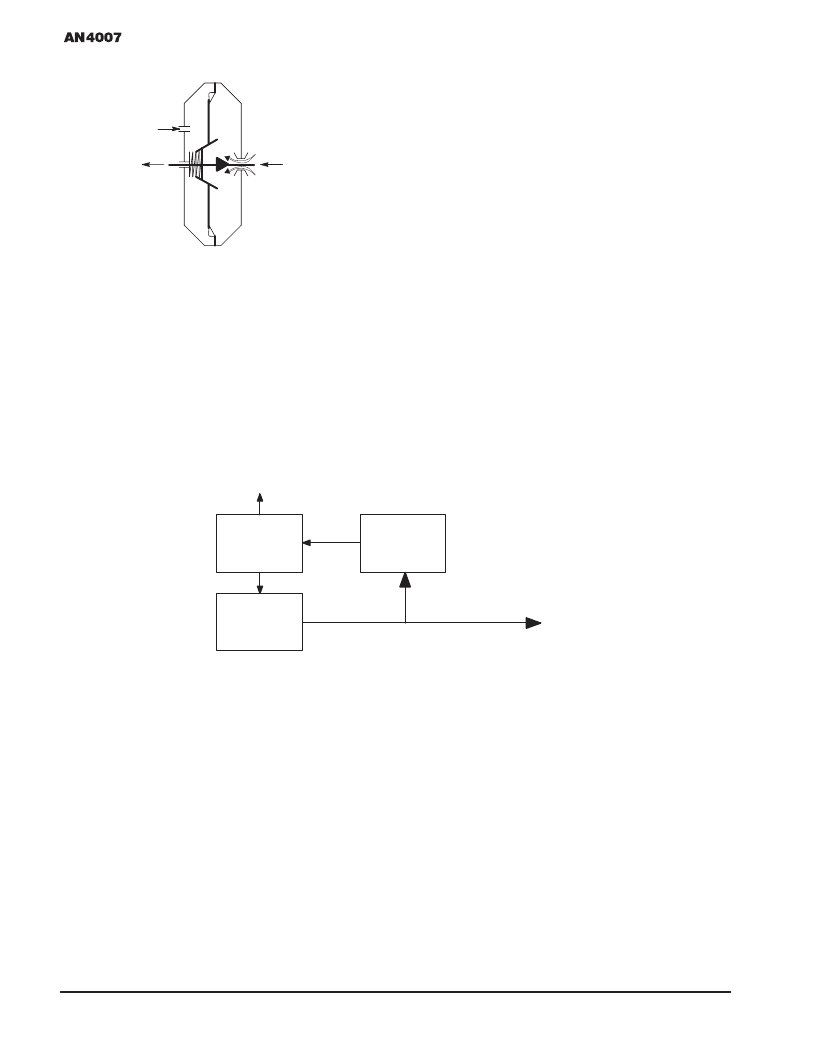
3–414
Motorola Sensor Device Data
For More Information On This Product,
Go to: www.freescale.com
Figure 2. Braking Phase
Fp
Pv
Fp + Fb
Pw
Once the brake pedal is activated (force Fp), the vacuum
valve is closed and the air intake valve is open proportionally
to the displacement of the push rod (Figure 2). The working
chamber is progressively open to atmospheric pressure,
which creates a differential between the vacuum chamber and
the working chamber. This differential pressure applied to the
surface (S) of the piston results in a force Fb = (Pw – Pv) x S
.
The forces Fb + Fp are then applied to the brake pads through
the master cylinder and hydraulic links.
When the brake pedal is released, the spring moves the
piston back, closing the air intake valve and opening the
vacuum valve to rebalance the pressure between the two
chambers.
VACUUM GENERATION
On most passenger cars, vacuum is generated by the
engine itself. When the engine throttle valve is closed, the
displacement of the pistons produces vacuum in the intake
manifold. Thanks to a tube or hose connected between the
engine intake manifold and the brake booster, vacuum can be
applied to the chambers. A backslash valve inserted between
the intake manifold and the booster maintains the vacuum in
the booster when the engine throttle valve is open.
This principle has some limitations, however. For example,
it can be only used on engines that have the ability to generate
enough vacuum. On diesel engines, which have no throttle
valve, it is necessary to use an auxiliary pump to generate
vacuum. This will also be the case on the Gasoline Direct
Injection (GDI) engine, where in some driving conditions (idle,
lean burn) the electrically assisted throttle valve will be
maintained slightly open. In this situation, the vacuum
available on the intake manifold is not sufficient to provide an
efficient braking.
Figure 3. Vacuum Pump Monitoring
PUMP CONTROL
CIRCUIT
ELECTRICAL
VACUUM
PUMP
VACUUMFEEDBACK
VACUUMGENERATION
PRESSURE
SENSOR
BUS INTERFACE
Therefore, it is necessary and desirable to use an electrical
pump that will generate the vacuum for the brake booster. The
use of an auxiliary electrical pump (Figure 3) provides several
advantages over the “intake manifold” vacuum.
Vacuum generation is no longer related to the engine
running condition. Vacuum is only generated and con-
trolled by the pump thanks to a vacuum pressure sensor
that provides an accurate reading to the pump electrical
control circuit.
The electrical pump can be switched on and off based on
the required vacuum. To compensate atmospheric pres-
sure variation in order to maintain a constant booster
effect, the pump also can be switched on independently
from the atmospheric pressure. Various algorithms for
driving the pump can be implemented depending on the
required braking conditions.
Pressure variations during braking can be measured,
and the pump can be activated to generated additional
vacuum if required to increase the braking force.
Leakage can be detected by the pressure sensors and
the pump can be switched on to compensate them. The
driver can be informed of any type of failure thanks to the
bus interface. Vacuum level, and thus available braking
force can be communicated through the bus to other
braking systems such as, for example, ABS or ESP.
Motorola,
semiconductors, has introduced a new integrate pressure
sensor dedicated to vacuum measurements in applications
such as brake booster monitoring. The single–chip vacuum
sensor may be placed directly onto the pump electronic
control unit or integrated as component within the brake
booster, thus providing flexibility, system integration and
reduced system cost.
a
worldwide
leader
in
automotive
F
Freescale Semiconductor, Inc.
n
.