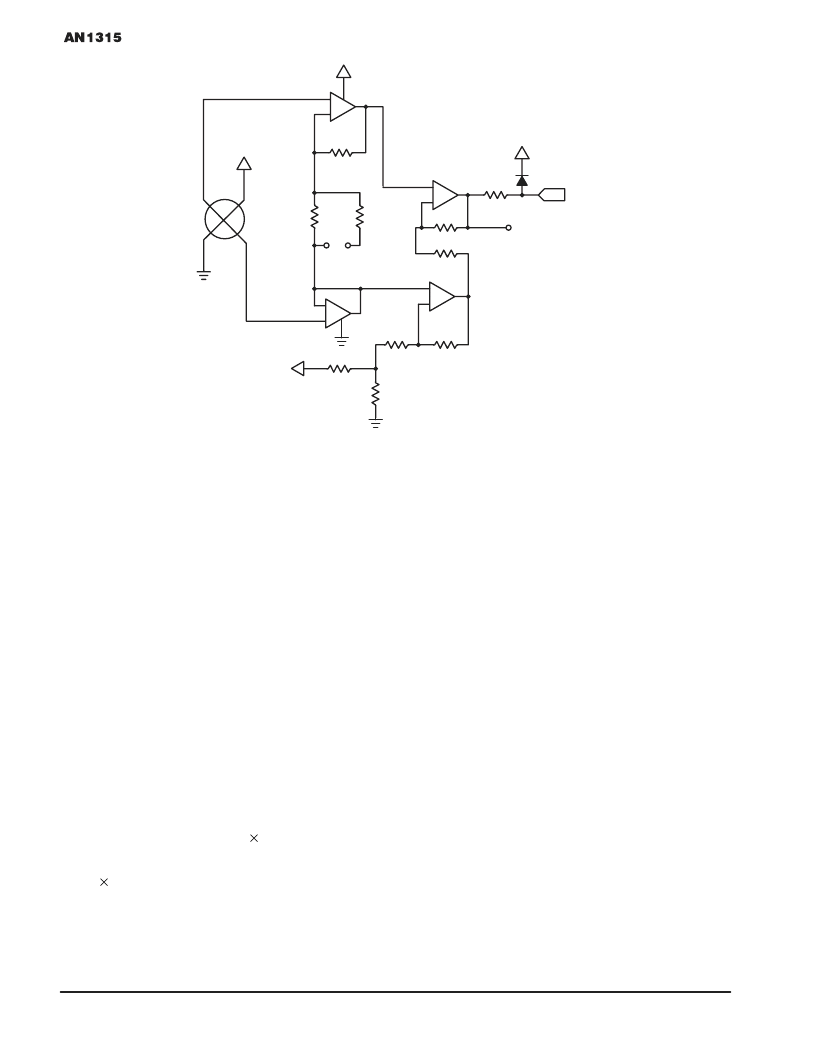
3–248
Motorola Sensor Device Data
For More Information On This Product,
Go to: www.freescale.com
–
+
U1A
–
+
U1C
–
+
U1D
+
–
U1B
PD0
TP1
+5 V
1N914
4.7K
R4
8
10
9
R5
2K
R6
2K
14
12
13
3
2
11
1
976
R9
1K
R10
340
R7
R8
23.7
+8
+8
1
XDCR1
4
2
3
121
R2
200
R3
6.98K
R1
5
6
47
+12 V
MC33274
D2
J8 IS INSTALLED FOR
THE MPX2010 ONLY
J8
Figure 3.
Figure 4. Analog Interface
Referring to Figure 4, most of the amplification of the voltage
from the pressure sensor is provided by U1A which is
configured as a differential amplifier. U1B serves as a unity
gain buffer in order to keep any current that flows through R2
(and R3) from being fed back into the sensor’s negative
output. With zero pressure applied to the sensor, the
differential voltage from pin 2 to pin 4 of the sensor is zero or
very close to zero volts. The common mode, or the voltage
measured between pins 2 or 4 to ground, is equal to
approximately one half of the voltage applied to the sensor, or
4 volts. The zero pressure output voltage at pin 7 of U1A will
then be 4 volts because pin 1 of U1B is also at 4 volts, creating
a zero bias between pins 5 and 6 of U1A. The four volt zero
pressure output will then be level shifted to the desired zero
pressure offset voltage (approximately 0.7 volts) by U1C and
U1D.
To further explain the operation of the level shifting circuitry,
refer again to Figure 4. Assuming zero pressure is applied to
the sensor and the common mode voltage from the sensor is
4 volts, the voltage applied to pin 12 of U1D will be 4 volts,
implying pin 13 will be at 4 volts. The gain of amplifier U1D will
be (R10/(R8+R9)) +1 or a gain of 2. R7 will inject a Voffset (0.7
volts) into amplifier U1D, thus causing the output at U1D pin
14 to be 7.3 = (4 volts @ U1D pin 12 2) – 0.7 volts. The gain
of U1C is also set at 2 ((R5/R6)+1). With 4 volts applied to pin
10 of U1C, its output at U1C pin 8 will be 0.7 = ((4 volts @ U1C
pin 10
2) – 7.3 volts). For this scheme to work properly,
amplifiers U1C and U1D must have a gain of 2 and the output
of U1D must be shifted down by the Voffset provided by R7. In
this system, the 0.7 volts Voffset was arbitrarily picked and
could have been any voltage greater than the Vsat of the op
amp being used. The system software will take in account any
variations of Voffset as it assumes no pressure is applied to the
sensor at system power up.
The gain of the analog circuit is approximately 117. With the
values shown in Figure 4, the gain of 117 will provide a span
of approximately 4 volts on U1C pin 8 when the pressure
sensor and the 8 volt fixed voltage regulator are at their
maximum output voltage tolerance. All of the sensors listed in
Table 1 with the exception of the MPX2010DP output
approximately 33 mV when full scale pressure is applied.
When the MPX2010DP sensor is used, its full scale sensor
differential output is approximately 20 mV. J8 must be installed
to increase the gain of the analog circuit to still provide the 4
volts span out of U1C pin 8 with a 20 mV differential from the
sensor.
Diode D2 is used to protect the microprocessor’s A/D input
if the output from U1C exceeds 5.6 volts. R4 is used to provide
current limiting into D4 under failure or overvoltage conditions.
SOFTWARE
The source code, compiled listing, and S–record output for
the software used in this system are available on the Motorola
Freeware Bulletin Board Service in the MCU directory under
the filename DEVB158.ARC. To access the bulletin board,
you must have a telephone line, a 300, 1200 or 2400 baud
modem and a personal computer. The modem must be
compatible with the Bell 212A standard. Call (512) 891–3733
to access the Bulletin Board Service.
Figure 5 is a flowchart for the program that controls the
system. The software for the system consists of a number of
modules. Their functions provide the capability for system
calibration as well as displaying the pressure input to the
MPX2000 series pressure sensor.
F
Freescale Semiconductor, Inc.
n
.