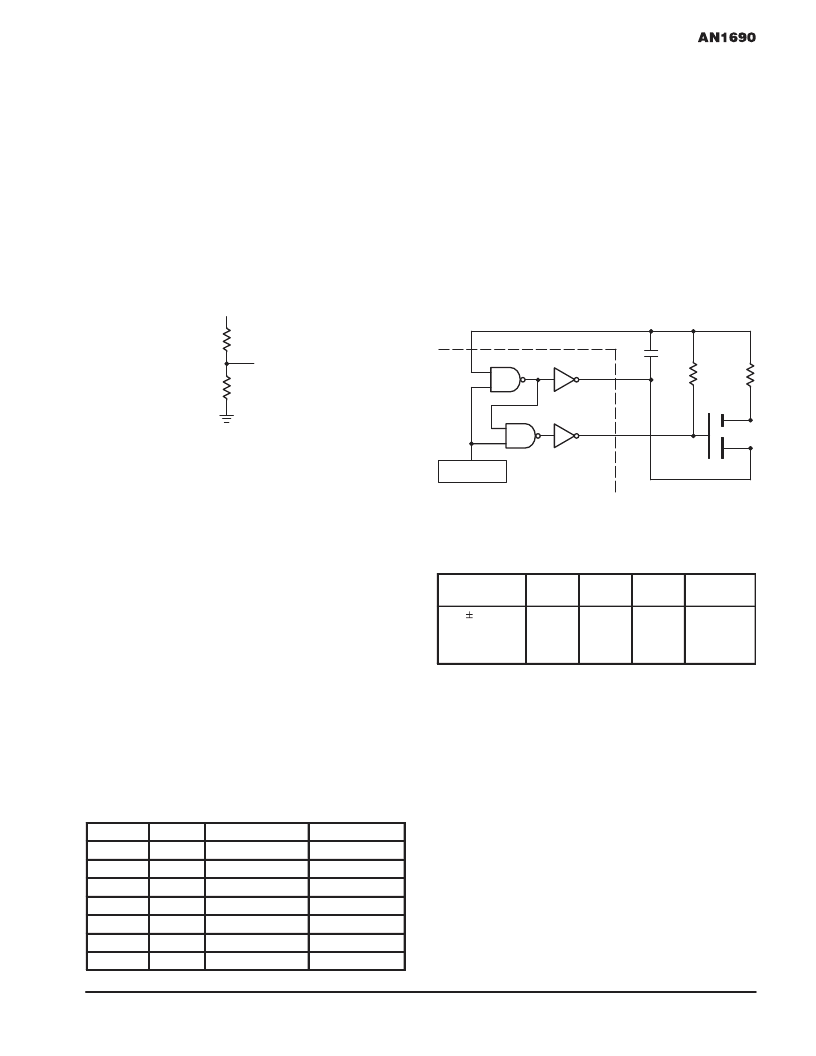
4–67
Motorola Sensor Device Data
For More Information On This Product,
Go to: www.freescale.com
ALARM THRESHOLD ADJUSTMENTS
The alarm trigger point (alarm threshold) is set externally to
any voltage level with a simple voltage divider connected to
pin 13. For instance, to connect the Alarm IC to a sensor that
has an output of 1.0 V during a no alarm condition and 4.0 V
during an alarm condition, the alarm threshold voltage could
be set to 3.0 V using a 2 M
and a 1 M
resistor connected
between VDD and ground (See Figure 3). Pin 13 connects
internally to the negative input of the Detect Comparator.
Based on the input impedance of the Detect Comparator the
maximum suggested total resistance for the threshold voltage
divider is 10 M
.
Figure 3. Alarm Threshold Voltage Divider
VDD
2 M
1 M
PIN 13
OSCILLATOR
The master clock frequency for the MC14600 is determined
by the external components Rbias (pin 7) and Cosc (pin 12).
This RC network provides the timing for the various functions
conducted by the IC. The oscillator timing affects the period
between LED pulses, alarm signal sampling, and the horn out-
put pulses and power consumption. A standard RC network
for the MC14600 oscillator uses an 8.2 M resistor (Rbias) con-
nected from VDD to pin 7 and a 0.1 uF capacitor (Cosc) con-
nected from pin 12 to ground. This configuration will provide
a period of approximately 1.65 sec in standby and 41.67 msec
in alarm. A change in oscillator speed is accomplished by
changing the resistor and capacitor values previously stated.
Changing the oscillator timing will not change the horn pattern
but it will change the speed at which it’s delivered. The table
below lists examples of RC values and measured sampling
periods achieved with those values (deviation from theoretical
values are due to tolerance in components).
Table 1. Oscillator Period vs. Rbias and Cosc Value
Rbias
5.6 M
8.2 M
10 M
5.6 M
8.2 M
10 M
8.2 M
Cosc
0.01
μ
F
0.01
μ
F
0.01
μ
F
0.1
μ
F
0.1
μ
F
0.1
μ
F
1.0
μ
F
Period (no alarm)
93 msec
Period (alarm)
2.3 msec
142 msec
3.4 msec
172 msec
3.9 msec
1.4 sec
32 msec
2.2 sec
50 msec
2.7 sec
60 msec
20.1 sec
456 msec
PIEZO HORN INTERFACE
The MC14600 contains on–board horn driver circuitry to
drive three leaded piezo horns. A three leaded horn is consid-
ered self–driven, having a feedback pin that is connected to
a closed loop oscillation circuit. The MC14600 uses pin 8
(Horn Feedback), pin 10 (Horn Out 1) and pin 11 (Horn Out 2)
to interface to a piezo horn and achieve the drive circuit. Pin
10 and pin 11 alternate their output providing the oscillation for
the horn. Three external components are required to interface
a piezo horn to the Alarm IC:
R1
,
C1
and
R2
(Figure 4). R1 is
usually around 1.5 M
and is the least critical component as
it only biases the horn. R2 and C1 are critical to achieve maxi-
mum horn output. The two components must be set so that the
value of 1/(R2*C1) is close to the resonant frequency of the
horn being used. Table 2 lists a common horn frequency and
potential external components that can be used for R2 and C1.
Figure 4. Piezo Horn Interface to MC14600
FDBK
8
R2
R1
C1
11
OUT 2
ALARMLOGIC
10
OUT 1
Table 2. External Components for a 3.4 kHz
Three Leaded Piezo Horn
Horn Osc.
Frequency
R1
R2
C1
1/(R2*C1)
3.33 kHz
3.33 kHz
3.79 kHz
4.55 kHz
3.4
0.4 kHz
1.5 M
820 k
1.5 M
1.5 M
200 k
200 k
120 k
100 k
1.5 nF
1.5 nF
2.2 nF
2.2 nF
LOW BATTERY THRESHOLD ADJUSTMENTS
The Alarm IC has a typical internal low battery reference
voltage of 6 V. An internal resistor divider string provides a volt-
age of 80% of VDD which is compared to the 6 V reference volt-
age (See Figure 5). This results in a low battery condition and
horn chirp if the VDD level is decreased to approximately 7.5 V.
The percentage of VDD that is compared can be changed by
adding a resistor to pin 3. A resistor from pin 3 to VDD will lower
the percentage while a resistor from pin 3 to GND will increase
the percentage. The low battery comparator information will
be latched only during the LED pulse. Testing of the voltage
at pin 3 should be done during the LED pulse for confirmation.
It should also be measured through a high impedance buffer
to avoid altering the voltage level.
ALARM LATCHING APPROACHES
There are detection applications where the event that trig-
gers the alarm can be instantaneous, such as shock or motion.
F
Freescale Semiconductor, Inc.
n
.