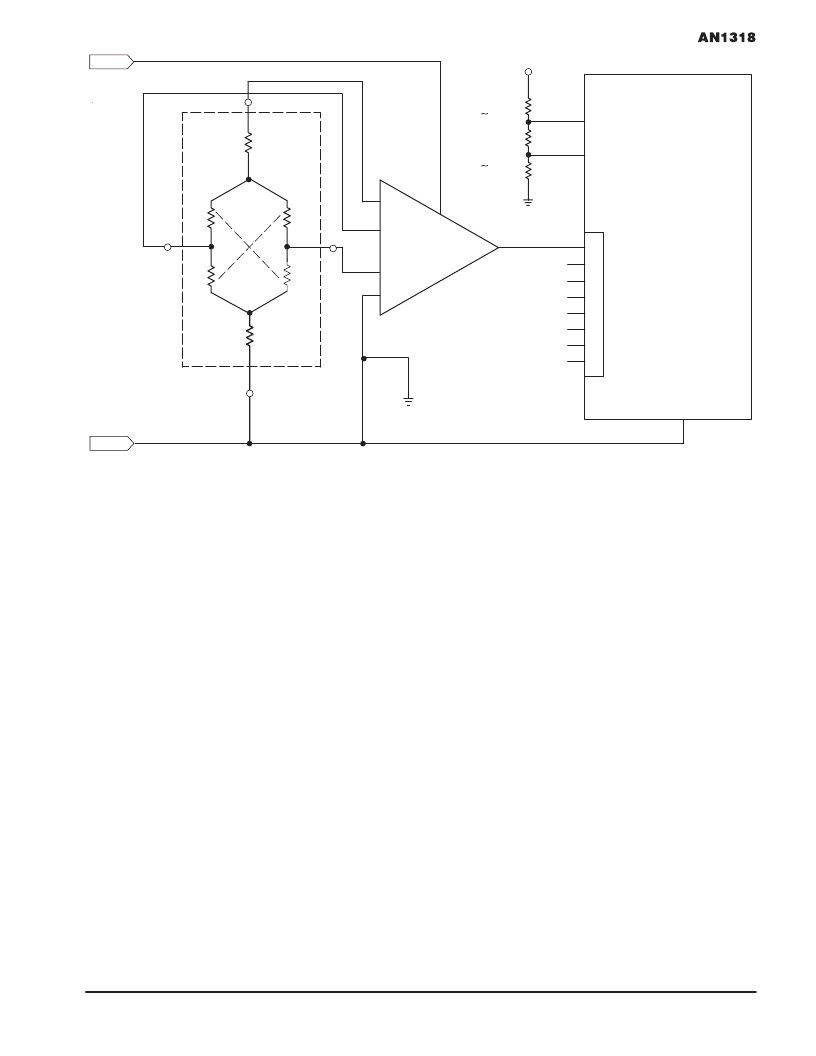
3–273
Motorola Sensor Device Data
For More Information On This Product,
Go to: www.freescale.com
Figure 6. Application Example
RETURN
B+
RC1
RV1
S+
RP1
RP2
RV2
S–
RC2
BIAS
+
—
B+
INTERFACE
AMPLIFIER
OUTPUT
GND
GND
VREFH
VREFL
+5 V
15.0 OHMS
1%
30.1 OHMS
1%
4.85 V
.302 V
453 OHMS
1%
0
1
2
3
4
5
6
7
PORT E
MC68HC11
VSS
MPX2000
SERIES
PRESSURE
SENSOR
VS
Beginning with the ramp generator, a timing ramp is
generated with current source U5 and capacitor C3.
Initialization is provided by Q1 which sets the voltage on C3
at approximately ground. With the values shown, 470
μ
A
flowing into 0.47
μ
F provide approximately a 5 msec ramp time
from zero to 5 V. Assuming zero pressure on the sensor, inputs
to both comparators U2A and U2B are at the same voltage.
Therefore, as the ramp voltage sweeps from zero to 5 V, both
PA0 and PA1 will go low at the same time when the ramp
voltage exceeds the common mode voltage. The processor
counts the number of clock cycles between the time that PA0
and PA1 go low, reading zero for zero pressure.
In this circuit, U4A and U4B form the front end of an
instrument amplifier. They differentially amplify the sensor’s
output. The resulting amplified differential signal is then
sampled and held in U1 and U3. The sample and hold function
is performed in order to keep input data constant during the
conversion process. The stabilized signals coming out of U1
and U3 feed a higher output voltage to U2A than U2B,
assuming that pressure is applied to the sensor. Therefore,
the ramp will trip U2B before U2A is tripped, creating a time
difference between PA0 going low and PA1 going low. The
processor reads the number of clock cycles between these
two events. This number is then linearly scaled with software
to represent the amplified output voltage, accomplishing the
analog to digital conversion.
When the ramp reaches the reference voltage established
by R9 and R10, comparator U2C is tripped, and a reset
command is generated. To accomplish reset, Q1 is turned on
with an output from PA7, and the sample and hold circuits are
delatched with an output from PB1. Resolution is limited by
clock frequency and ramp linearity. With the ramp generator
shown in Figure 7 and a clock frequency of 2 MHz; resolution
is 11 bits.
From a software point of view, the A/D conversion consists
of latching the sample and hold, reading the value of the
microcomputer’s free running counter, turning off Q1, and
waiting for the three comparator outputs to change state from
logic 1 to logic 0. The analog input voltage is determined by
counting, in 0.5
μ
sec steps, the number of clock cycles
between PA0 and PA1 going low.
LONG DISTANCE INTERFACES
In applications where there is a significant distance between
the sensor and microcomputer, two types of interfaces are
typically used. They are frequency output and 4–20 mA loops.
In the frequency output topology, pressure is converted into a
zero to 5 V digital signal whose frequency varies linearly with
pressure. A minimum frequency corresponds to zero pressure
and above this, frequency output is determined by a Hz/unit
pressure scaling factor. If minimizing the number of wires to a
remote sensor is the most important design consideration,
4–20 mA current loops are the topology of choice. These loops
utilize power and ground as the 4–20 mA signal line and
therefore require only two wires to the sensor. In this topology
4 mA of total current drain from the sensor corresponds to zero
pressure, and 20 mA to full scale.
F
Freescale Semiconductor, Inc.
n
.