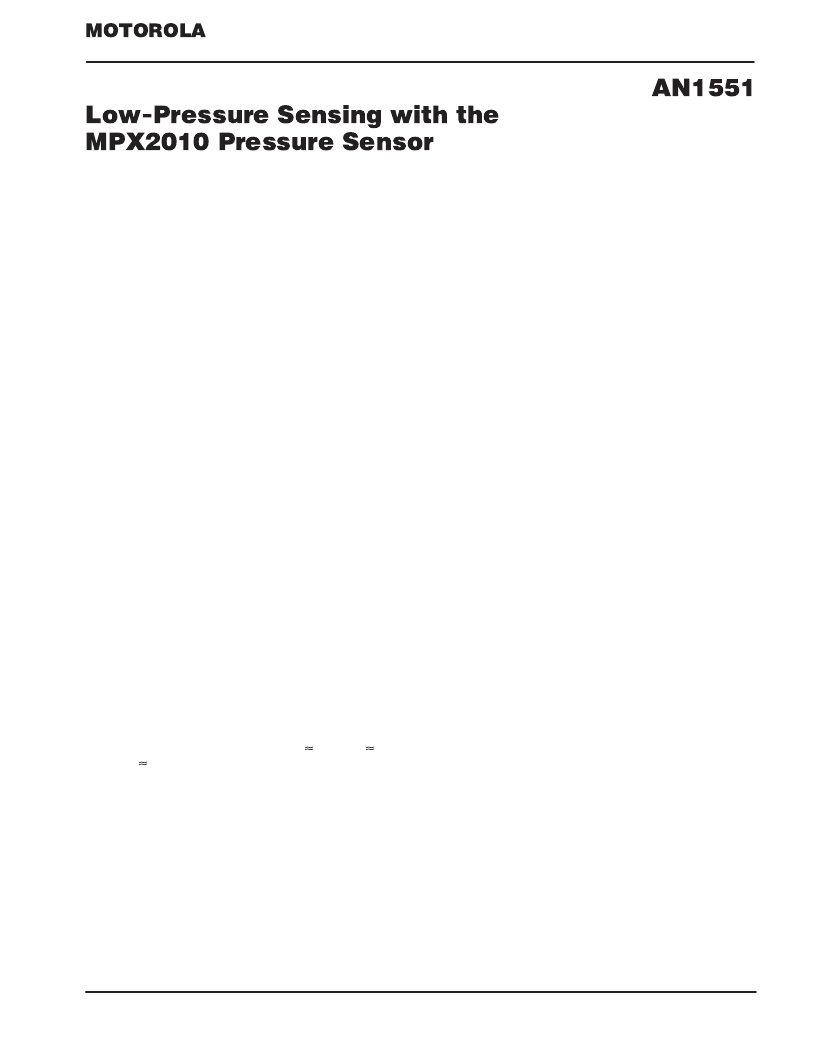
3–337
Motorola Sensor Device Data
For More Information On This Product,
Go to: www.freescale.com
Prepared by: Jeffery Baum
Systems Engineering Group Leader
Sensor Products Division
Motorola Semiconductor Products Sector
Phoenix, AZ
INTRODUCTION
Until recently, low–cost semiconductor pressure sensors
were designed to measure typical full–scale pressures only as
low as 10 kPa (1.5 psi). Of course, “measure” is a relative term.
“Measure” is used here to imply that an output of reasonable
magnitude, signal–to–noise ratio, and accuracy is produced
by the sensing device. Such sensor products are available in
various levels of integration and package types. Depending
on the level of application customization required and the
budget available, a sensor user may choose from a range of
low–pressure sensor products such as a 10 kPa
“bare–element” (uncompensated) device, a 10 kPa calibrated
and
temperature
compensated
signal–conditioned (high–level output), calibrated, and
temperature compensated integrated 10 kPa device. These
options are typically available as well for higher pressures
ranging up to 1000 kPa.
What if the sensor user must measure full–scale pressures
that are two, four, or even ten times lower than what
conventional sensor technology is capable of measuring “Do
such applications and customers exist’’ The answer is “yes”
and “yes.” There are many potential customers that require
such low–pressure sensing ability, the two application
examples discussed here are: (1) heating ventilation and
air–conditioning (HVAC) in the context of building controls and
(2) water–level sensing in appliance applications such as
clothes washing machines.
For the purposes of measuring low pressures, the units of
inches of water (
″
H2O) or millimeters of water (mm H2O) will
be used. Typical HVAC applications have a full–scale
pressure of 40 mm H2O and washing machines have either
300 or 600 mm H2O, depending on the region of the world
(Note:just for reference purposes, 10 kPa
40
″
H2O
mm H2O
1.5 psi).
Of course, a sensor intended for a higher pressure range
than the one of interest can be used. However, the effect is that
only a small portion on the device’s dynamic output range is
used for the actual operating range. This low–level output may
then be paired up with a larger than ideal amplifier gain. Thus,
a poor signal–to–noise ratio is usually the result. Some sensor
manufacturers have recently introduced pressure sensors
designed for 4
″
and 5
″
H2O full–scale ranges (approx.
100–125 mm H2O). These devices typically employ silicon
with very thinly micromachined diaphragms or other sensing
technologies that are significantly larger in form factor without
any additional functionality. Thin diaphragm devices tend to be
extremely fragile and unstable. Even in cases where the
device is sufficiently robust for the intended operating
device,
or
a
fully
1000
pressure range, the sensor has very poor overpressure
capability.
Now that the pressure range of interest has been
established, the stage has been set to consider the system
solution that is the enabling technology for achieving such
low–pressure sensing capability. Also important in presenting
this low–pressure system solution are some of the other
application characteristics besides the pressure range. For
example, the desired pressure resolution, accuracy, available
power supply voltage, and end–equipment system
architecture play a major role in determining the
implementation of this system solution.
DEVELOPMENT HISTORY
For simplicity’s sake, let’s refer to this low–pressure sensing
system solution as the “smart sensing” or “smart sensor
system.” One of the key performance advantages of the smart
sensor system is that the output of the actual sensing element
is ratiometric (linearly proportional) to the excitation voltage
applied to the sensing element. Since most semiconductor
pressure sensors are characterized with a constant voltage
power supply, current excitation will not be discussed.
Although a sensor’s operation is specified at a given power
supply voltage, there is some maximum supply that can be
applied, beyond which power dissipation and self–heating
produce significant output errors or exceed the package’s
thermal handling capability. This means that the strategy of
increasing the sensor’s excitation to improve the sensor’s
sensitivity (increase signal output for a given applied pressure)
can be done in a dc fashion only up to some maximum supply
voltage. For Motorola pressure sensors, this limit allows only
about a 50% to 60% increase in sensitivity, depending on the
specific device family.
About five years ago, some of my colleagues were working
on pulsing the sensor supply voltage with a conventional
voltage and very low duty–cycle, sampling–and–holding the
resulting output, and then filtering the output to produce a dc
sensor output with very low–power consumption. This was the
impetus to consider pulsing a sensor at a much higher than
recommended voltage and a low duty–cycle (10% or less) for
the purpose of increased sensitivity. It is true that some of the
sensor’s parasitic drawbacks, like its zero–pressure offset
voltage and temperature coefficient of offset, are increased as
well, but some of the sensor’s negative characteristics are
lessened. In addition, other sources of error and noise in the
system are not subjected to the higher amplifier gain that
would be required if operating the sensor at a conventional
supply voltage.
SEMICONDUCTOR APPLICATION NOTE
F
Freescale Semiconductor, Inc.
n
.