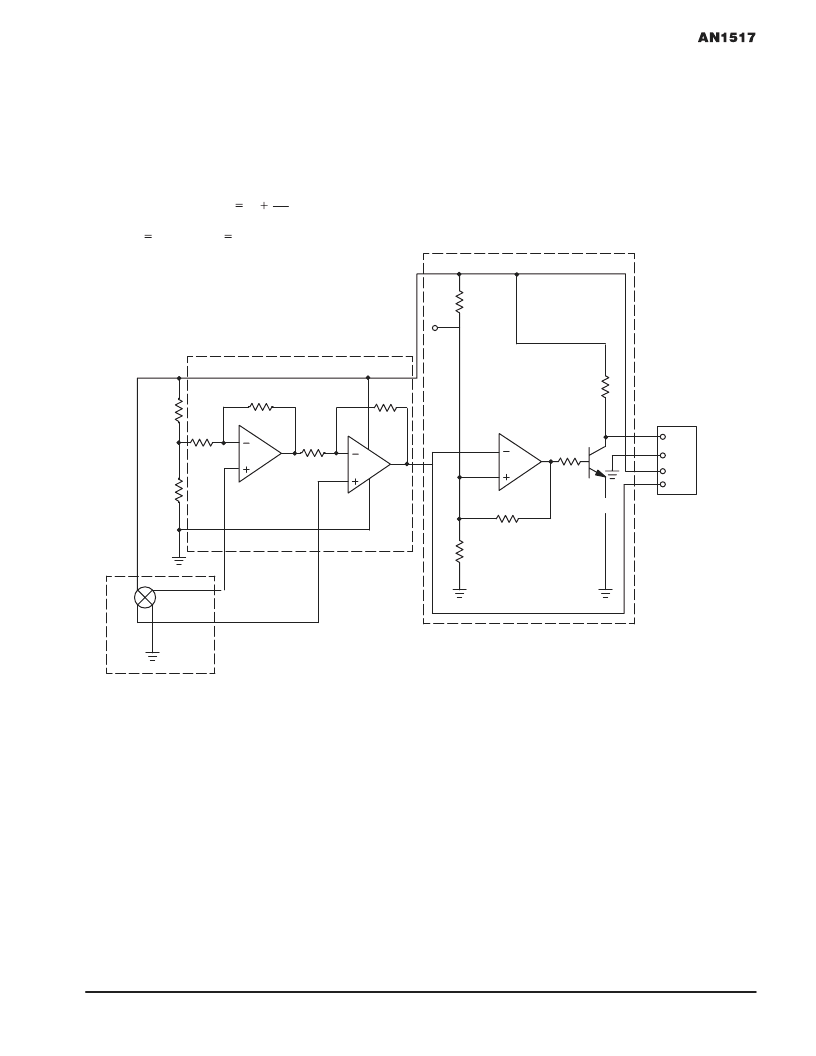
3–307
Motorola Sensor Device Data
For More Information On This Product,
Go to: www.freescale.com
THE SIGNAL CONDITIONING
The amplifier circuitry, shown in Figure
1, is composed of
two op–amps. This interface circuit has a much lower
component count than conventional quad op amp
instrumentation amplifiers. The two op amp design offers the
high input impedance, low output impedance, and high gain
desired for a transducer interface, while performing a
differential to single–ended conversion. The gain is set by the
following equation:
GAIN
1
R6
R5
where R6
R3 and R4
R5.
For this specific design, the gain is set to 201 by setting
R6 = 20 k
and R5 = 100
. Using these values and setting
R6 = R3 and R4 = R5 gives the desired gain without loading
the reference voltage divider formed by R1 and Roff. The offset
voltage is set via this voltage divider by choosing the value of
Roff. This enables the user to adjust the offset for each
application’s requirements.
Figure 1. Pressure Switch Schematic
Amplifier Stage
Comparator Stage
R1
12.1 k
R4
100
R5
100
R6
20 k
Roff
X1
MPX2100DP
2
Pressure Sensor
RTH
10 k
RH
121 k
R10
24.3 k
R7
10.0 k
R11
4.75 k
Q1
MMBT3904LT1
U1
U1
LM324D
VTH
CN1
Vout
GND
+5 V
V4
R3
20 k
U1
3 4
1
THE COMPARISON STAGE
The comparison stage is the “heart” of the pressure switch
design. This stage converts the analog voltage output to a
digital output, as dictated by the comparator’s threshold. The
comparison stage has a few design issues which must be
addressed:
The threshold for which the output switches must be pro-
grammable. The threshold is easily set by dividing the sup-
ply voltage with resistors R7 and RTH. In Figure 1, the
threshold is set at 2.5 V for R7 = RTH = 10 k
.
A method for providing an appropriate amount of hystere-
sis should be available. Hysteresis prevents multiple tran-
sitions from occurring when slow varying signal inputs
oscillate about the threshold. The hysteresis can be set by
applying positive feedback. The amount of hysteresis is
determined by the value of the feedback resistor, RH (refer
to equations in the following section).
It is ideal for the comparator’s logic level output to swing
from one supply rail to the other. In practice, this is not pos-
sible. Thus, the goal is to swing as high and low as possible
for a given set of supplies. This offers the greatest differ-
ence between logic states and will avoid having a micro-
controller read the switch level as being in an indeterminate
state.
In order to be compatible with CMOS circuitry and to avoid
microcontroller timing delay errors, the comparator must
switch sufficiently fast.
By using two comparators, a window comparator may be
implemented. The window comparator may be used to
monitor when the applied pressure is within a set range. By
adjusting the input thresholds, the window width can be
customized for a given application. As with the single
F
Freescale Semiconductor, Inc.
n
.