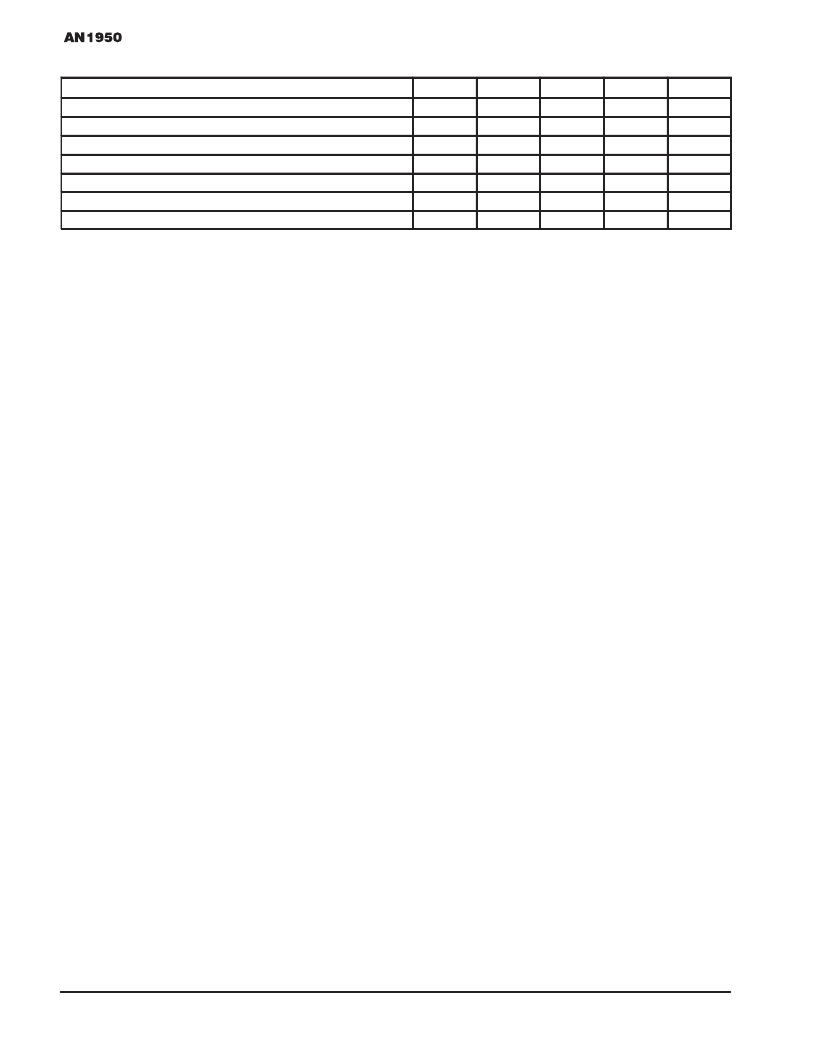
3–396
Motorola Sensor Device Data
For More Information On This Product,
Go to: www.freescale.com
Table 1: MPXM2010D OPERATING CHARACTERISTICS
(VS = 10 Vdc, TA = 25
°
C unless otherwise noted, P1 > P2)
Characteristic
Pressure Range(1)
Supply Voltage(2)
Symbol
Min
Typ
Max
Unit
POP
VS
Io
VFSS
Voff
V/
P
0
—
10
kPa
—
10
16
Vdc
Supply Current
Full Scale Span(3)
Offset(4)
—
6.0
—
mAdc
24
25
26
mV
–1.0
—
1.0
mV
Sensitivity
Linearity(5)
—
2.5
—
mV/kPa
—
–1.0
—
1.0
%VFSS
Amplifier Selection and Amplifier Induced Errors
The sensor output needs to be amplified before being
inputted directly to the microcontroller through an 8–bit A/D
input pin. To determine the amplification requirements, the
pressure sensor output characteristics and the 0–5V input
range for the A/D converter had to be considered.
The amplification circuit uses three op–amps to add an
offset and convert the differential output of the MPXM2010GS
sensor to a ground–referenced, single–ended voltage in the
range of 0 – 5V.
The pressure sensor has a possible offset of +/– 1mV at the
minimum rated pressure. To avoid a nonlinear response when
a pressure sensor chosen for the system has a negative offset
(Voff), we have added a 5mV offset to the positive sensor
output signal. This offset will remain the same regardless of
the sensor output. Any additional offset that the sensor or
op–amp introduce is compensated for by software routines
that are invoked when the initial system calibration is done.
To determine the gain required for the system, the maximum
output voltage from the sensor for this application had to be
determined. The maximum output voltage from the sensor is
approximately 12.5mV with a 5V supply since the full–scale
output of the sensor changes linearly with supply voltage. This
system will have a maximum pressure of 4kPa at 40cm of
water. At a 5V supply, we will have a maximum sensor output
of 5mV at 4kPa of pressure. To amplify the maximum sensor
output to 5.0V, the following gain is needed:
Gain = (Max Output needed) / (Max Sensor Output and
Initial Offset)
= 5.0V / (.005V + .005) = 500
The gain for the system was set for 500 to avoid railing from
possible offsets from the pressure sensor or the op–amp.
The Voltage Outputs from the sensor are each connected
to a non–inverting input of an op–amp. Each op–amp circuit
has the same resistor ratio. The amplified voltage signal from
the negative sensor lead is VA. The resulting voltage is
calculated as follows:
VA= (1+R8/R6) * V4
= (1+10/1000) * V4
= (1.001) * V4
The amplified voltage signal from the positive sensor lead
is VB. This amplification adds a small gain to ensure that the
positive lead, V2, is always greater than the voltage output
from the negative sensor lead, V4. This ensures the linearity
of the differential voltage signal.
VB = (1+R7/R5) * V2 – (R7/R5) * Vcc
= (1+10/1000) * V2 + (10/1000)*(5V)
= (1.001) * V2 + .005V
The difference between the positive sensor voltage, VB, and
the negative sensor voltage, VA is calculated and amplified
with a resulting by a gain of 500.
VC= (R12/R11) * (VB – VA)
= (500K/1K) * (VB – VA)
= 500 * (VB – VA)
The output voltage, Vc, is connected to a voltage follower.
Therefore, the resulting voltage, Vc, is passed to an A/D pin
of the microcontroller.
The range of the A/D converter is 0 to 255 counts. However,
the A/D Values that the system can achieve are dependent on
the maximum and minimum system output values:
Count = (Vout – VRL) / ( VRH – VRL) x 255
where VXdcr = Transducer Output Voltage
Vrh = Maximum A/D voltage
Vlh = Minimum A/D voltage
Count (0mm H20) = (2.5 – 0) / (5.0 – 0) x 255 = 127
Count (40mm H20) = (5.0 – 0) / (5.0 – 0) x 255 = 255
Total # counts = 255 – 127 = 127 counts.
The resolution of the system is determined by the mm of
water that is represented by each A/D count. As calculate
above, the system has a span of 226 counts to represent water
level up to and including 40cm. Therefore, the resolution is:
Resolution = mm of water / Total # counts
= 400mm/127 counts = 3.1 mm per A/D count
F
Freescale Semiconductor, Inc.
n
.