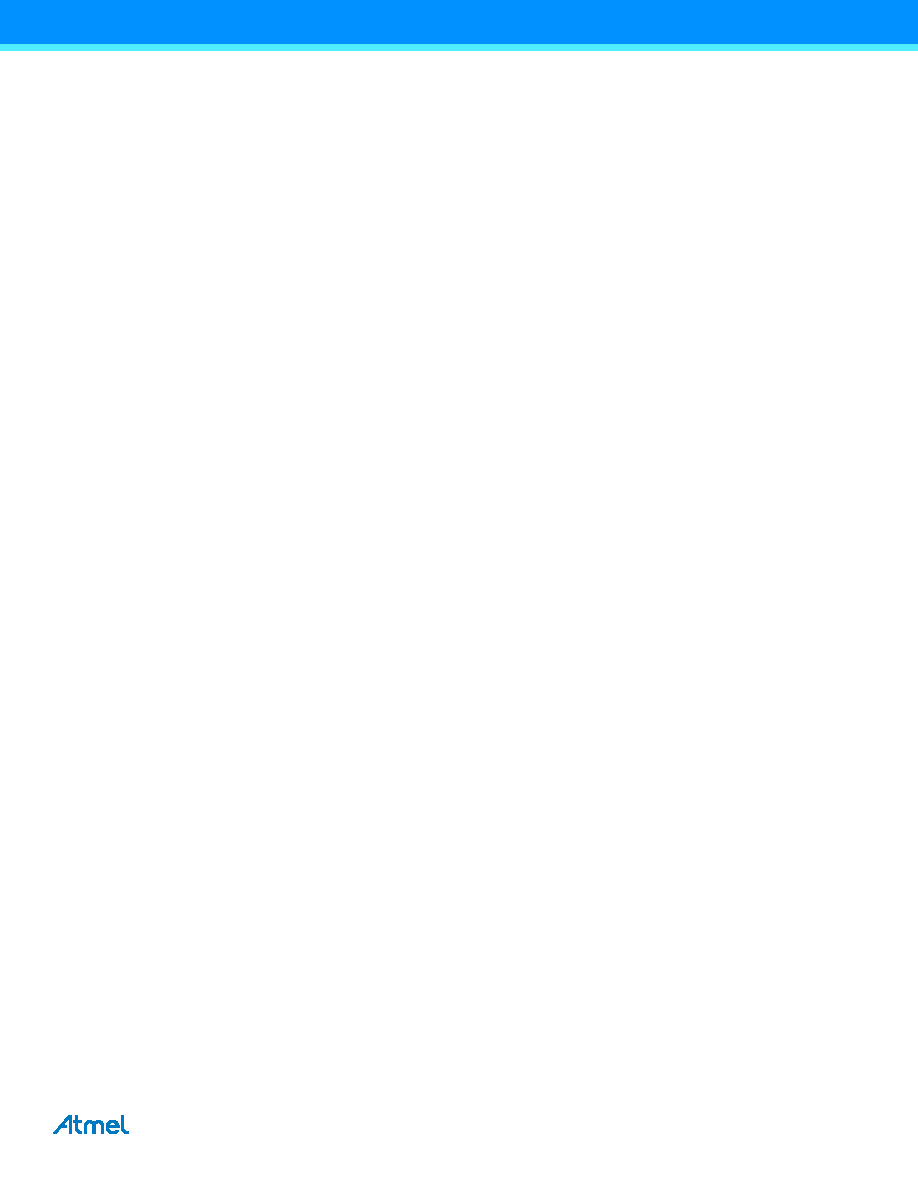
190
ATmega16M1/32M1/64M1 [DATASHEET]
8209E–AVR–11/2012
20. LIN / UART - Local Interconnect Network Controller or UART
20.1
Features
20.1.1
LIN
Hardware implementation of LIN 2.1 (LIN 1.3 Compatibility)
Small, CPU efficient and independent Master/Slave routines based on “LIN Work Flow Concept” of LIN 2.1
specification
Automatic LIN header handling and filtering of irrelevant LIN frames
Automatic LIN response handling
Extended LIN error detection and signalling
Hardware frame time-out detection
“Break-in-data” support capability
Automatic re-synchronization to ensure proper frame integrity
Fully flexible extended frames support capabilities
20.1.2
UART
Full duplex operation (independent serial receive and transmit processes)
Asynchronous operation
High resolution baud rate generator
Hardware support of eight data bits, odd/even/no parity bit, and one stop bit frames
Data over-run and framing error detection
20.2
Overview
The LIN (Local Interconnect Network) is a serial communications protocol which efficiently supports the control of
mechatronics nodes in distributed automotive applications. The main properties of the LIN bus are:
Single master with multiple slaves concept
Low cost silicon implementation based on common UART/SCI interface
Self synchronization in slave node
Deterministic signal transmission with signal propagation time computable in advance
Low cost single-wire implementation
Speed up to 20Kbit/s
LIN provides a cost efficient bus communication where the bandwidth and versatility of CAN are not required. The
specification of the line driver/receiver needs to match the ISO9141 NRZ-standard.
If LIN is not required, the controller alternatively can be programmed as Universal Asynchronous serial Receiver
and Transmitter (UART).
20.3
LIN protocol
20.3.1
Master and slave
A LIN cluster consists of one master task and several slave tasks. A master node contains the master task as well
as a slave task. All other nodes contain a slave task only.