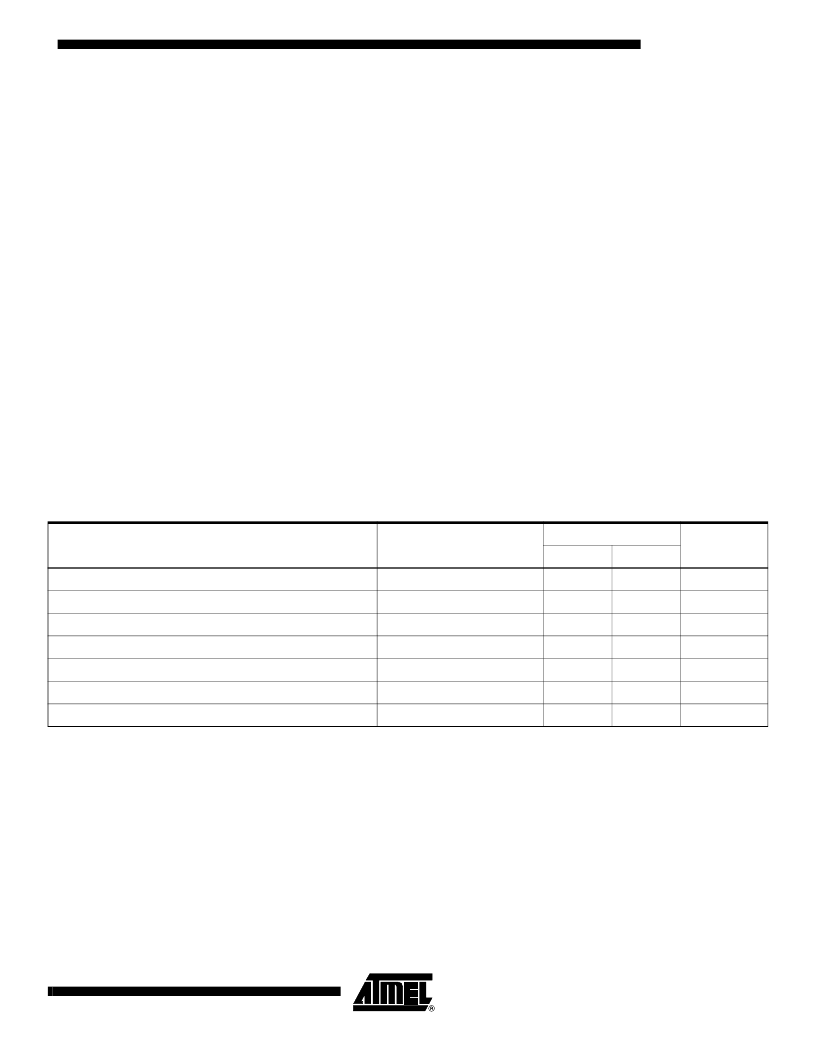
29
PC755/745
2138D–HIREL–06/03
Motorola is similarly limited by system constraints and cannot perform tests of the L2
interface on a socketed part on a functional tester at the maximum frequencies of Table
15. Therefore functional operation and AC timing information are tested at core-to-L2
divisors of 2 or greater. Functionality of core-to-L2 divisors of 1 or 1.5 is verified at less
than maximum rated frequencies.
L2 input and output signals are latched or enabled respectively by the internal L2CLK
(which is SYSCLK multiplied up to the core frequency and divided down to the L2CLK
frequency). In other words, the AC timings of Table 16 and Table 17 are entirely inde-
pendent of L2SYNC_IN. In a closed loop system, where L2SYNC_IN is driven through
the board trace by L2SYNC_OUT, L2SYNC_IN only controls the output phase of
L2CLKOUTA and L2CLKOUTB which are used to latch or enable data at the SRAMs.
However, since in a closed loop system L2SYNC_IN is held in phase alignment with the
internal L2CLK, the signals of Table 16 and Table 17 are referenced to this signal rather
than the not-externally-visible internal L2CLK. During manufacturing test, these times
are actually measured relative to SYSCLK.
The L2SYNC_OUT signal is intended to be routed halfway out to the SRAMs and then
returned to the L2SYNC_IN input of the PC755 to synchronize L2CLKOUT at the SRAM
with the processor’s internal clock. L2CLKOUT at the SRAM can be offset forward or
backward in time by shortening or lengthening the routing of L2SYNC_OUT to
L2SYNC_IN. See Motorola Application Note AN179/D “PowerPC
Backside L2 Timing
Analysis for the PCB Design Engineer.”
The L2CLKOUTA and L2CLKOUTB signals should not have more than two loads.
Notes:
1. L2CLK outputs are L2CLK_OUTA, L2CLK_OUTB, L2CLK_OUT and L2SYNC_OUT pins. The L2CLK frequency to core fre-
quency settings must be chosen so that the resulting L2CLK frequency and core frequency do not exceed their respective
maximum or minimum operating frequencies. The maximum L2LCK frequency will be system dependent. L2CLK_OUTA
and L2CLK_OUTB must have equal loading.
2. The nominal duty cycle of the L2CLK is 50% measured at midpoint voltage.
3. The DLL re
-
lock time is specified in terms of L2CLKs. The number in the table must be multiplied by the period of L2CLK to
compute the actual time duration in nanoseconds. Re
-
lock timing is guaranteed by design and characterization.
4. The L2CR[L2SL] bit should be set for L2CLK frequencies less than 110 MHz. This adds more delay to each tap of the DLL.
5. Allowable skew between L2SYNC_OUT and L2SYNC_IN.
6. This output jitter number represents the maximum delay of one tap forward or one tap back from the current DLL tap as the
phase comparator seeks to minimize the phase difference between L2SYNC_IN and the internal L2CLK. This number must
be comprehended in the L2 timing analysis. The input jitter on SYSCLK affects L2CLKOUT and the L2 address/data/control
signals equally and therefore is already comprehended in the AC timing and does not have to be considered in the L2 timing
analysis.
7. Guaranteed by design.
Table 15. L2CLK Output AC Timing Specification.
At
V
DD
= A
V
DD
= 2.0V 100 mV; -55
≤
T
j
≤
+125
°
C, OV
DD
= 3.3V
165 mV and OV
DD
= 1.8V 100 mV and OV
DD
= 2.0V 100 mV
Parameter
Symbols
All Speed Grades
Unit
Min
Max
L2CLK frequency
(1)(4)
f
L2CLK
80
450
MHz
L2CLK cycle time
t
L2CLK
2.5
12.5
ns
L2CLK duty cycle
(2)(7)
t
CHCL
/t
L2CLK
45
55
%
Internal DLL
-
relock time
(3)(7)
–
640
–
L2CLK
DLL capture window
(5)(7)
–
0
10
ns
L2CLKOUT output
-
to
-
output skew
(6)(7)
t
L2CSKW
–
50
ps
L2CLKOUT output jitter
(6)(7)
–
–
±150
ps