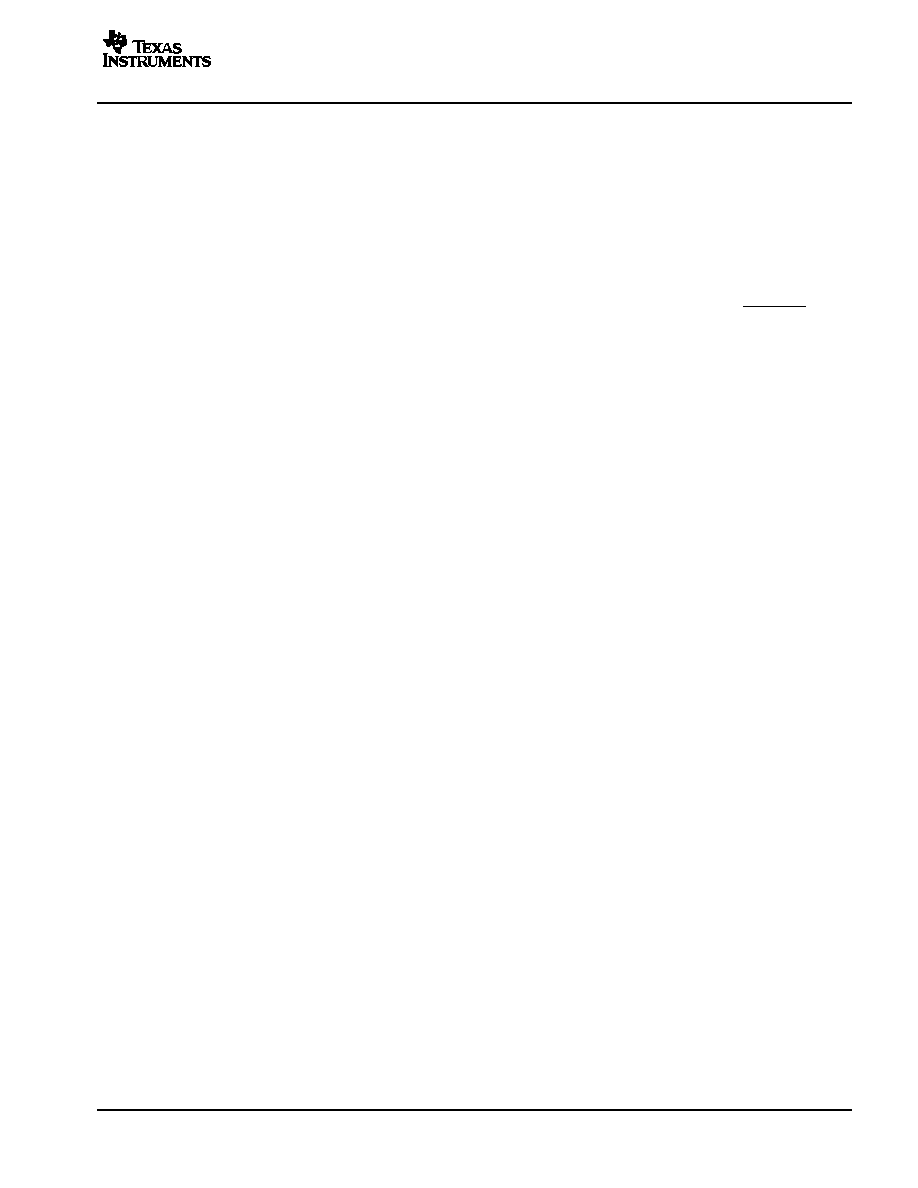
TSC2100
SLAS378 NOVEMBER 2003
www.ti.com
17
In some applications, external capacitors may be required across the touch screen for filtering noise picked up by the touch
screen, i.e. noise generated by the LCD panel or back-light circuitry. The value of these capacitors provides a low-pass
filter to reduce the noise, but causes an additional settling time requirement when the panel is touched.
Several solutions to this problem are available in the TSC2100. A programmable delay time is available which sets the
delay between turning the drivers on and making a conversion. This is referred to as the panel voltage stabilization time,
and is used in some of the modes available in the TSC2100. In other modes, the TSC2100 can be programmed to turn
on the drivers only without performing a conversion. Time can then be allowed before the command is issued to perform
a conversion.
The TSC2100 touch screen interface can measure position (X, Y) and pressure (Z). Determination of these coordinates
is possible under three different modes of the A/D converter: (1) conversion controlled by the TSC2100, initiated by
detection of a touch; (2) conversion controlled by the TSC2100, initiated by the host responding to the PINTDAV signal;
or (3) conversion completely controlled by the host processor.
Touch Screen A/D Converter
The analog inputs of the TSC2100 are shown in
Figure 17. The analog inputs (X, Y, and Z touch panel coordinates, battery
voltage monitors, chip temperature and auxiliary input) are provided via a multiplexer to the successive approximation
register (SAR) analog-to-digital (A/D) converter. The A/D architecture is based on a capacitive redistribution architecture,
which inherently includes a sample/hold function.
A unique configuration of low on-resistance switches allows an unselected A/D input channel to provide power and an
accompanying pin to provide ground for driving the touch panel. By maintaining a differential input to the converter and a
differential reference input architecture, it is possible to negate errors caused by the driver switch on-resistances.
The A/D is controlled by an A/D converter control register. Several modes of operation are possible, depending upon the
bits set in the control register. Channel selection, scan operation, averaging, resolution, and conversion rate may all be
programmed through this register. These modes are outlined in the sections below for each type of analog input. The results
of conversions made are stored in the appropriate result register.