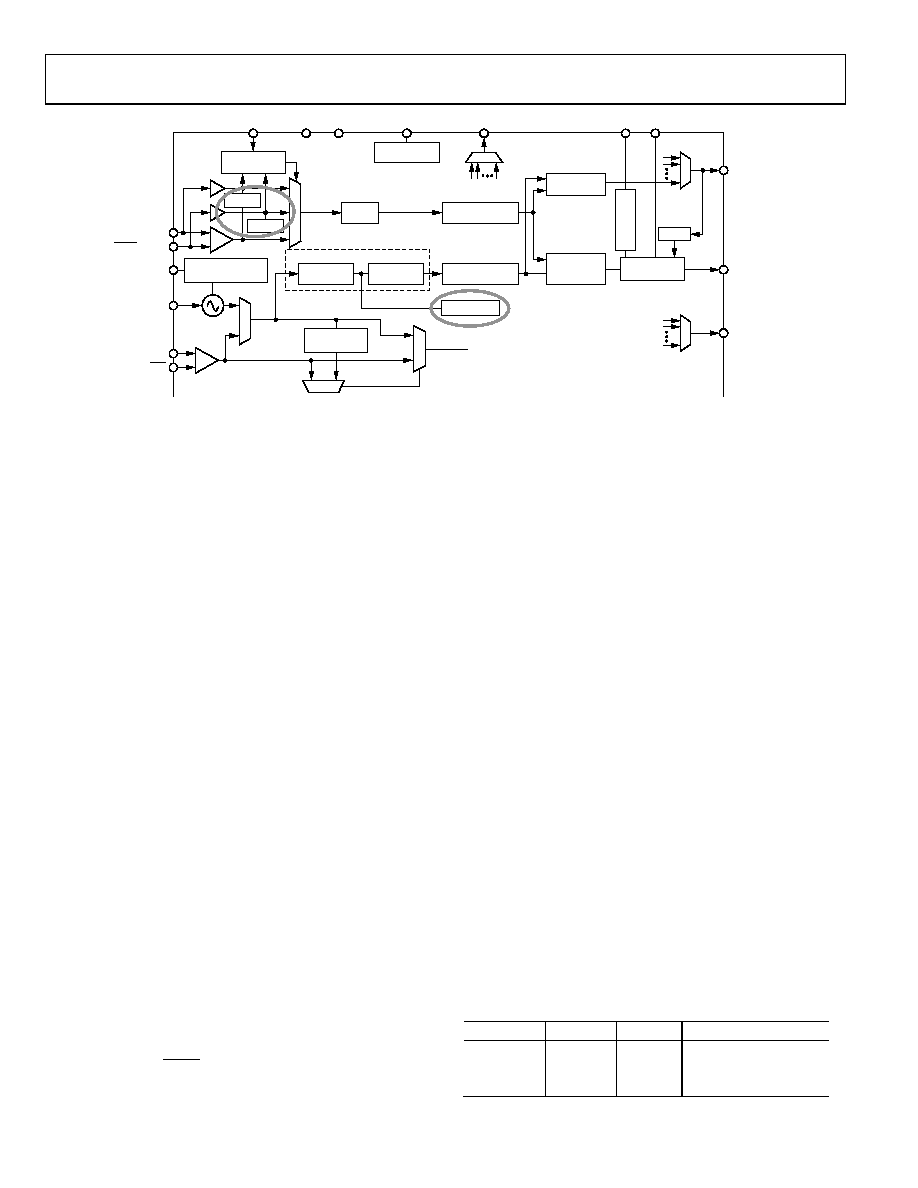
AD9517-1
Data Sheet
Rev. E | Page 40 of 80
PROGRAMMABLE
N DELAY
REFIN (REF1)
REFIN (REF2)
CLK
REF1
REF2
STATUS
R
DIVIDER
VCO STATUS
PROGRAMMABLE
R DELAY
REFERENCE
SWITCHOVER
REF_SEL
CPRSET VCP
VS
GND
RSET
DISTRIBUTION
REFERENCE
REFMON
CP
STATUS
LD
P, P + 1
PRESCALER
A/B
COUNTERS
N DIVIDER
BYPASS
LF
LOW DROPOUT
REGULATOR (LDO)
VCO
PHASE
FREQUENCY
DETECTOR
LOCK
DETECT
CHARGE
PUMP
PL
L
RE
F
E
RE
NCE
HOLD
0
1
0
1
DIVIDE BY
2, 3, 4, 5, OR 6
06
425-
0
70
Figure 54. Reference and VCO Status Monitors
VCO Calibration
operation over process and temperature. VCO calibration centers
the dc voltage at the internal VCO input (at the LF pin) for the
selected configuration; this is normally required only during initial
configuration and any time the PLL settings change. VCO calibra-
tion is controlled by a calibration controller driven by the R divider
output. The calibration requires that the input reference clock be
present at the REFIN pins, and that the PLL be set up properly to
lock the PLL loop. During the first initialization after a power-up or
a reset of th
e AD9517, a VCO calibration sequence is initiated by
setting Register 0x018[0] = 1b. This can be done during initial
setup, before executing an update registers (Register 0x232[0] =
1b). Subsequent to initial setup, a VCO calibration sequence is
initiated by resetting Register 0x018[0] = 0b, executing an update
registers operation, setting Register 0x018[0] = 1b, and executing
another update registers operation. A readback bit, Bit 6 in
Register 0x1F, indicates when a VCO calibration is finished
by returning a logic true (that is, 1b).
The sequence of operations for the VCO calibration is as follows:
1.
Program the PLL registers to the proper values for the PLL
loop. Note that that automatic holdover mode must be
disabled, and the VCO divider must not be set to “Static.”
2.
Ensure that the input reference signal is present.
3.
For the initial setting of the registers after a power-up or reset,
initiate VCO calibration by setting Register 0x018[0] = 1b.
Subsequently, whenever a calibration is desired, set
Register 0x018[0] = 0b, update registers; and then set
Register 0x018[0] = 1b, update registers.
4.
A sync operation is initiated internally, causing the outputs
to go to a static state determined by normal sync function
operation.
5.
The VCO calibrates to the desired setting for the requested
VCO frequency.
6.
Internally, the SYNC signal is released, allowing outputs to
continue clocking.
7.
The PLL loop is closed.
8.
The PLL locks.
A sync is executed during the VCO calibration; therefore, the
outputs of th
e AD9517 are held static during the calibration,
which prevents unwanted frequencies from being produced.
However, at the end of a VCO calibration, the outputs may
resume clocking before the PLL loop is completely settled.
The VCO calibration clock divider is set as shown i
n Table 54(Register 0x018[2:1]).
The calibration divider divides the PFD frequency (reference
frequency divided by R) down to the calibration clock. The
calibration occurs at the PFD frequency divided by the
calibration divider setting. Lower VCO calibration clock
frequencies result in longer times for a calibration to be
completed.
The VCO calibration clock frequency is given by
fCAL_CLOCK = fREFIN/(R × cal_div)
where:
fREFIN is the frequency of the REFIN signal.
R is the value of the R divider.
cal_div is the division set for the VCO calibration divider
(Register 0x018[2:1]).
The VCO calibration takes 4400 calibration clock cycles.
Therefore, the VCO calibration time in PLL reference clock
cycles is given by
Time to Calibrate VCO =
4400 × R × cal_div PLL Reference Clock Cycles
Table 29. Example Time to Complete a VCO Calibration
with Different fREFIN Frequencies
fREFIN (MHz)
R Divider
PFD
Time to Calibrate VCO
100
1
100 MHz
88 μs
10
1 MHz
8.8 ms
10
100
100 kHz
88 ms