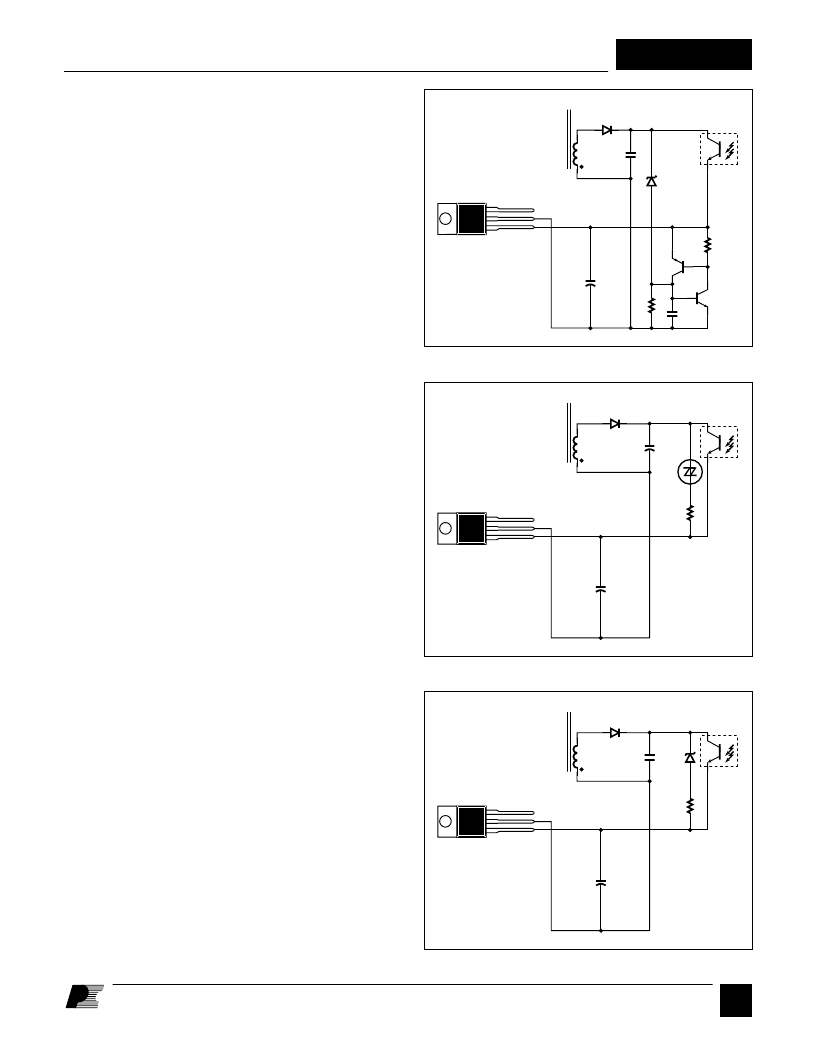
B
6/96
AN-14
17
10. Current to Duty Cycle Conversion
TOPSwitch
is a voltage-mode device that produces a duty cycle
inversely proportional to Control pin current.
TOPSwitch
is not
a current-mode device. Increasing Control pin current will
linearly decrease the duty cycle down to the minimum duty
cycle value. Further increases in Control pin current will have
no effect on the duty cycle until reaching the Latched Shutdown
Trigger Current (I
SD
) threshold at which point
TOPSwitch
shuts
down.
11. Minimum Duty Cycle Operation
TOPSwitch
internal supply current remains constant and does
not vary with duty cycle because of the minimum Duty Cycle
DC
. In some cases, a small pre-load may be necessary to
keep a lightly loaded or unloaded output voltage within the
desired range due to DC
. Shunt resistance or a Zener diode
with the proper power rating can simply be added across the
output voltage to provide preload current. Figure 2 shows how
R2 and VR2 provide minimum loading for the ST202A without
adding a large power component. R2 is a small, 1/8 Watt
resistor which passes minimum load current through the existing
500 mW Zener diode (VR2). Figure 3 shows a variable
minimum loading approach used on the ST204A. R2 dissipates
the most power when the power supply output is lightly loaded
and the TL431 (U3) output is saturated low to decrease
TOPSwitch
duty cycle. During normal operation, when wider
duty cycles are necessary,
TOPSwitch
Control pin current is
lower, TL431 output voltage is higher, R2 power dissipation is
lower, and overall efficiency is improved.
12. Control Loop
12.1 Basic Techniques
The
TOPSwitch
control function has two poles and a zero. One
pole is due to an internal RC filter with a typical corner
frequency of 7 kHz. This RC network filters switching noise
but contributes little phase shift at normal crossover frequencies
of 1 to 2 kHz. Auto-restart capacitor C5 (typically 47
μ
F)
together with the Control pin dynamic impedance (typically
15
) contributes the second pole of approximately 226 Hz. C5
as shown in Figure 11a has equivalent series resistance (typically
2
) which creates a zero at approximately 1.7 kHz. This
compensation method is used for power supplies operating in
discontinuous mode or lightly continuous mode at duty cycles
of 50% or less (such as the ST202A in Figure 2).
Additional series resistance R3 (between 2
and 15
) can be
added as shown in Figure 11b to move the zero lower in frequency.
This compensation method is used for power supplies operating
in continuous mode (such as the ST204A in Figure 3).
PI-1142A-081294
FROM
SECONDARY
BIAS
WINDING
47
μ
F
0.1
μ
F
DRAIN
SOURCE
CONTROL
PI-1141A-081294
FROM
SECONDARY
BIAS
WINDING
MBS4991
47
μ
F
1
μ
F
10
DRAIN
SOURCE
CONTROL
PI-1140A-081294
FROM
SECONDARY
BIAS
WINDING
1N5231B
47
μ
F
0.1
μ
F
47
DRAIN
SOURCE
CONTROL
Figure 8. Latching Overvoltage Protection Using an SCR.
Figure 9. Latching Overvoltage Using a Diac.
Figure 10. Bias Winding Regulator to Limit Output Voltage.