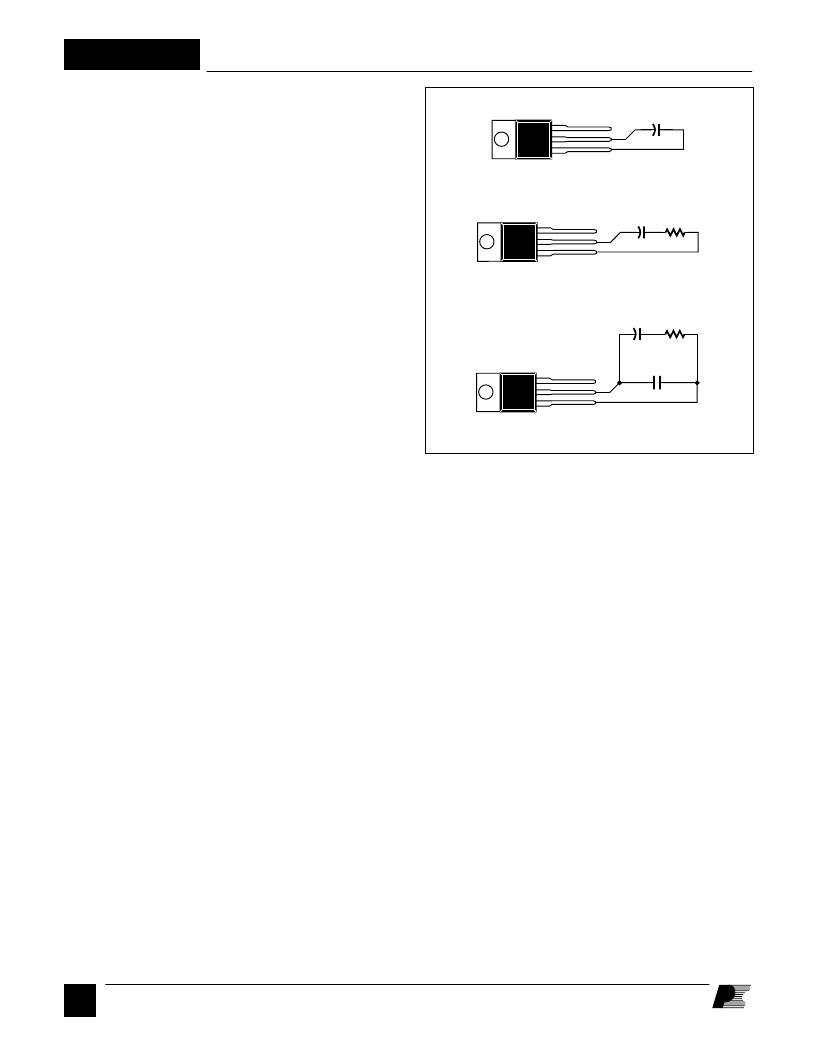
AN-14
18
B
6/96
12 Control Loop (continued)
R3 can be increased beyond 15
up to a maximum value of
100
to eliminate the effect of auto-restart capacitor C5 from
the control loop but bypass capacitor C10 must then be added
as shown in Figure 11c. This compensation method is good for
power supplies with sophisticated, secondary side compensation
schemes that do not require the dominant pole caused by auto-
restart capacitor C5.
R3 values beyond 100
are not
recommended
because auto-restart timing intervals will
decrease and auto-restart frequency will increase significantly.
In optocoupler feedback (such as the ST204A in Figure 3 and
the ST202A in Figure 2), series resistor R1 determines loop
gain. The initial value of R1 is selected using the following "5%
Rule": with the power supply operating at nominal line and full
load conditions, the average voltage across R1 should be
approximately 5% of the output voltage. To help compensate
the control loop, R1 can be increased above the 5% value to
reduce loop gain. In optocoupler circuits which use a Zener
diode (such as the ST202A circuit in Figure 2), reducing R1
below the 5% value will improve load regulation but will also
increase loop gain.
Stability can be examined with a step load change applied to the
power supply output. A current step from 75% to 100% of rated
output current is normally used. The voltage response is
observed for settling time and damping. In primary bias power
supplies, the bias voltage should be tested separately with a step
load change of 25% (typically 1 mA).
An LC postfilter effectively reduces output switching frequency
ripple voltage and high frequency noise but can cause circuit
instability due to additional phase shift. The ST202A power
supply (Figure 2) shows the proper connection for simple
Figure 11. Control Pin Compensation.
PI-1277-011895
DRAIN
SOURCE
CONTROL
C5
47
μ
F
DRAIN
SOURCE
CONTROL
C5
47
μ
F
R3
2.0
to
15
(a)
(b)
(c)
DRAIN
SOURCE
CONTROL
C5
47
μ
F
C10
0.1
μ
F
R3
15
to
100
.
optocoupler circuits (to the rectifier side of L1). The ST204A
power supply (Figure 3) shows the proper connection for
accurate optocoupler circuits. The optocoupler is connected to
the rectifier side of L1 but the resistor divider senses the voltage
directly at the power supply output which makes load regulation
independent of the DC resistance of L1. In this method, DC
feedback comes directly from the output while AC feedback
comes from before the postfilter to avoid additional phase shift.
12.2 TOPSwitchCircuit with Enhanced Bandwidth
Simple circuit improvements reduce output voltage line
frequency ripple and improve transient response in
TOPSwitch
power supplies using a TL431 shunt regulator and optocoupler
for control loop feedback. Figure 12 shows how the control
circuitry of a typical
TOPSwitch
power supply (such as the
ST204A Reference Design using the TOP204YAI) can be
easily modified to increase control loop gain and bandwidth
which reduces output voltage line frequency ripple while also
improving transient response. Reducing capacitance C9 down
to 0.01
μ
F improves TL431 frequency response. Increasing R3
to 13
improves loop phase margin. Adding 100 k
resistor
R6 as shown increases overall gain and also increases phase
margin.