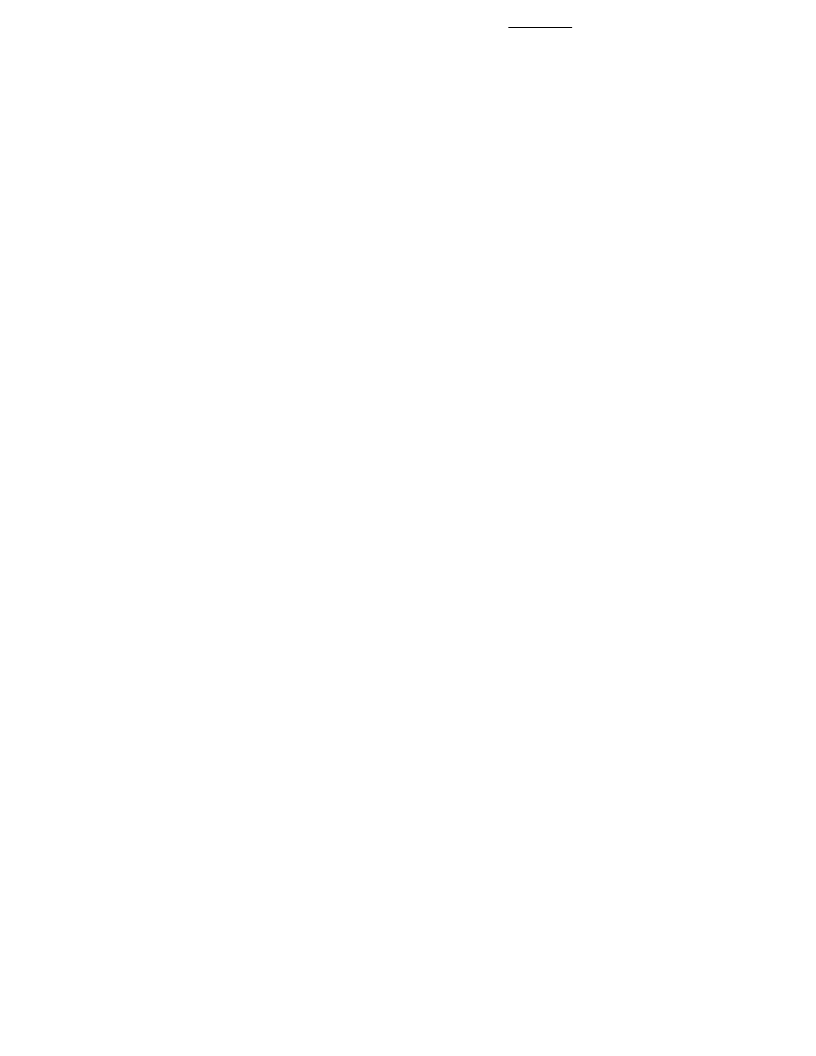
7
on the inside of the aperture on
all but the bottom side of the
shield and provides a good RF
connection to the panel. This
option can accommodate various
panel or enclosure thicknesses,
i.e. 1.02 mm (.04 in) min to 2.54 mm
(0.1 in) max. The reference plane
for this panel thickness variation is
from the front surface of the panel
or enclosure. The recommended
length for protruding the
HFBR/HFCT-5208EM transceiver
beyond the front surface of the
panel or enclosure is 6.35 mm
(0.25 in) . With this option, there
is flexibility of positioning the
module to fit the specific need of
the enclosure design. (See Figure
8 for the mechanical drawing
dimensions of this shield.)
The second shielded option,
option FM, is for applications that
are designed to have a flush
mounting of the module with
respect to the front of the panel or
enclosure. The flush-mount design
accommodates a large variety of
panel thickness, i.e. 1.02 mm
(.04 in) min to 2.54 mm (0.1 in)
max. Note the reference plane for
the flush-mount design is the
interior side of the panel or
enclosure. The recommended
distance from the centerline of
the transceiver front solder posts
to the inside wall of the panel is
13.82 mm (0.544 in) . This option
contacts the inside panel or
enclosure wall on all four sides of
this metal shield. (See Figure 10
for the mechanical drawing
dimensions of this shield.)
Both shielded design options
connect only to the equipment
chassis and not to the signal or
logic ground of the circuit board
within the equipment closure.
The front panel aperture
dimensions are recommended in
Figures 9 and 11. When layout of
the printed circuit board is done to
incorporate these metal-shielded
transceivers, keep the area on the
printed circuit board directly
under the external metal shield
free of any components and circuit
board traces. For additional EMI
performance advantage, use duplex
SC fiber-optic connectors that
have low metal content inside the
connector. This lowers the ability
of the metal fiber-optic connectors
to couple EMI out through the
aperture of the panel or enclosure.
Recommended Solder
and Wash Process
The HFBR/HFCT-5208M is
compatible with industry-standard
wave or hand solder processes.
HFBR-5000 Process Plug
The HFBR/HFCT-5208M
transceiver is supplied with a
process plug, the HFBR-5000, for
protection of the optical ports
receptacle. This process plug
prevents contamination during
wave solder and aqueous rinse as
well as during handling, shipping
or storage. It is made of high-
temperature, molded, sealing
material that will withstand
+80°C and a rinse pressure of
110 lb/in
2
.
Recommended Solder Fluxes
and Cleaning/Degreasing
Chemicals
Solder fluxes used with the
HFBR/HFCT-5208M fiber-optic
transceiver should be water-
soluble, organic solder fluxes.
Some recommended solder fluxes
are Lonco 3355-11 from London
Chemical West, Inc. of Burbank,
CA, and 100 Flux from Alpha-
metals of Jersey City, NJ
or
equivalent fluxes from other
companies.
Recommended cleaning and
degreasing chemicals for the
HFBR/HFCT-5208M are alcohols
(methyl, isopropyl, isobutyl),
aliphatics (hexane, heptane) and
other chemicals, such as soap
solution or naphtha. Do not use
partially halogenated
hydrocarbons for cleaning/
degreasing. Examples of
chemicals to avoid are 1,1.1
trichloroethane, ketones (such as
MEK), acetone, chloroform, ethyl
acetate, methylene dichloride,
phenol, methylene chloride or N
methylpyrolldone.
Regulatory Compliance
These transceiver products are
intended to enable commercial
system designers to develop
equipment that complies with the
various regulations governing
certification of Information
Technology Equipment. See the
Regulatory Compliance Table
for details. Additional information
is available from your Agilent
sales representative.
Electrostatic Discharge (ESD)
There are two design cases in
which immunity to ESD damage
is important.
The first case is during handling of
the transceiver prior to mounting
it on the circuit board. It is
important to use normal ESD
handling precautions for ESD
sensitive devices. These
precautions include using
grounded wrist straps, work
benches, and floor mats in ESD
controlled areas, etc.
The second case to consider is
static discharges to the exterior
of the equipment chassis
containing the transceiver parts.
To the extent that the duplex SC
connector receptacle is exposed
to the outside of the equipment
chassis, it may be subject to
whatever ESD system level test
criteria that the equipment is
intended to meet.