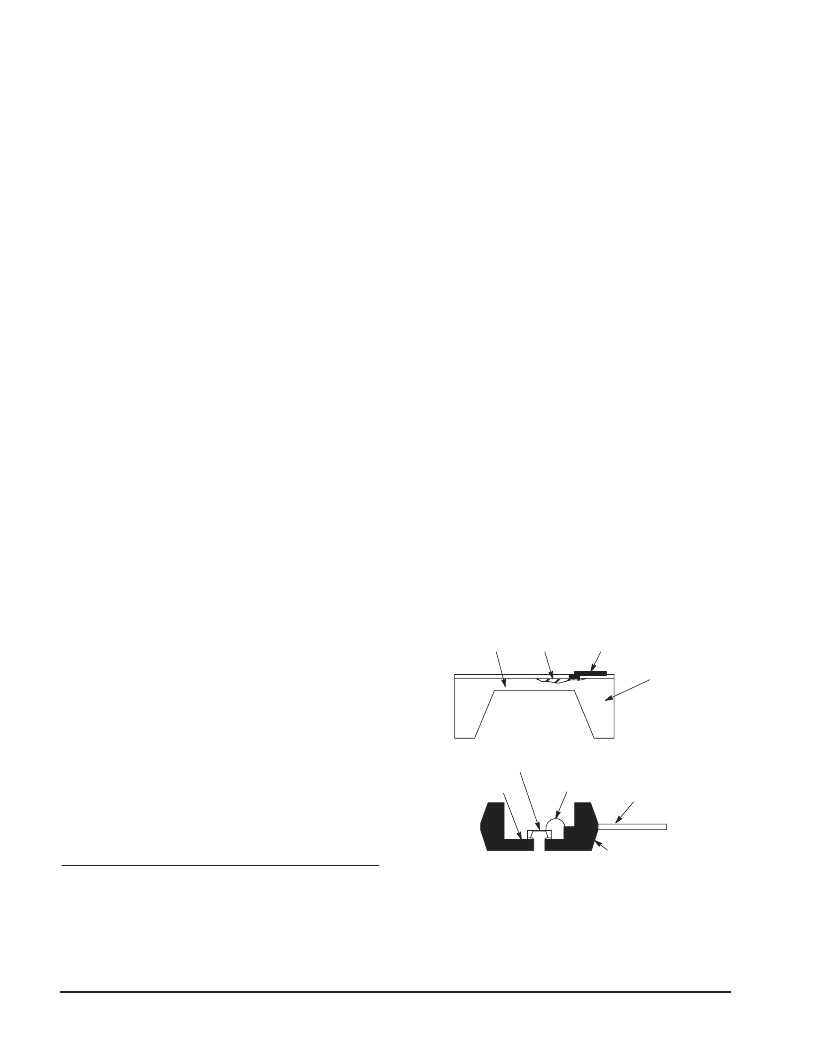
1–18
Motorola Sensor Device Data
For More Information On This Product,
Go to: www.freescale.com
Media Compatibility Disclaimer
Motorola has tested media tolerant sensor devices in
selected solutions or environments and test results are
based on particular conditions and procedures selected by
Motorola. Customers are advised that the results may vary
for actual services conditions. Customers are cautioned that
they are responsible to determine the media compatibility of
sensor devices in their applications and the foreseeable use
and misuses of their applications.
Sensor Media Compatibility: Issues and Answers
T. Maudie, D. J. Monk, D. Zehrbach, and D. Stanerson
Motorola Semiconductor Products Sector, Sensor Products Division
5005 E. McDowell Rd., Phoenix, AZ 85018
ABSTRACT
As sensors and actuators are embedded deeper into
electronic systems, the issue of media compatibility as well as
sensor and actuator performance and survivability becomes
increasingly critical. With a large number of definitions and
even more explanations of what media compatibility is, there
is a ground swell of confusion not only within the industry, but
among end users as well. The sensor industry must respond
to create a clear definition of what media compatibility is, then
strive to provide a comprehensive understanding and industry
wide agreement on what is involved in assessing media
tolerance and compatibility. Finally, the industry must create
a standard set of engineering parameters to design, evaluate,
test, and ultimately qualify sensor and actuators functioning in
various media conditions. This paper defines media
compatibility, identifies pertinent compatibility issues, and
recommends a path to industry standardization.
INTRODUCTION
Microelectromechanical System (MEMS) reliability in
various media is a subject that has not yet received much
attention in the literature yet [1–3], but does bring up many
potential issues. The effects of long term media exposure to
the silicon MEMS device and material still need answers [4].
Testing can result in predictable silicon or package related
failures, but due to the complexity of the mechanisms,
deleterious failures can be observed. The sensor may be
exposed to diverse media in markets such as automotive,
industrial, and medical. This media may include polar or
nonpolar organic liquids, acids, bases, or aqueous solutions.
Integrated circuits (ICs) have long been exposed to
temperature extremes, humid environments, and mechanical
tests to demonstrate or predict the reliability of the device for
the application. Unlike a typical IC, a sensor often must exist
in direct contact with a harsh environment. The lack of harsh
media simulation test standardization for these direct contact
situations necessitates development of methods and
hardware to perform reliability tests.
This paper was presented at Sensors Expo, Anaheim, CA, and is
reprinted with permission, Sensors Magazine (174 Concord St.,
Peterborough, NH 03458) and Expocon Management Associates,
Inc. (PO. Box 915, Fairfield, CT 06430).
The applicability of media compatibility affects all sensors to
some degree, but perhaps none more dramatically than a
piezoresistive pressure sensor. In order to provide an
accurate, linear output with applied pressure, the media
should come in direct contact with the silicon die. Any barrier
provided between the die and the media, limits the device
performance. A typical piezoresistive diaphragm pressure
sensor manufactured using bulk micromachining techniques
is shown in Figure 1. A definition for a media compatible
pressure sensor will be proposed.
To ensure accurate media testing, the requirements and
methods need to be understood, as well as what constitutes
a failure. An understanding of the physics of failure can
significantly reduce the development cycle time and produce
a higher quality product [5,6]. The focus of the
physics–of–failure approach includes the failure mechanism,
accelerating environment, and failure mode. The requirement
for a typical pressure sensor application involves long term
exposure to a variety of media at an elevated temperature and
may include additional acceleration components such as
static or cyclic temperature and pressure.
Figure 1. Typical bulk micromachined silicon
piezoresistive pressure sensor device
and package configuration.
ééé
DIE
RTV DIE BOND
ETCHED
CAVITY
METALLIZATION
EPOXY
CASE
WIRE
SILICON
WAFER
DIFFUSED
STRAIN GAUGE
DIAPHRAGM
LEAD
FRAME
INTERCONNECT
F
Freescale Semiconductor, Inc.
n
.