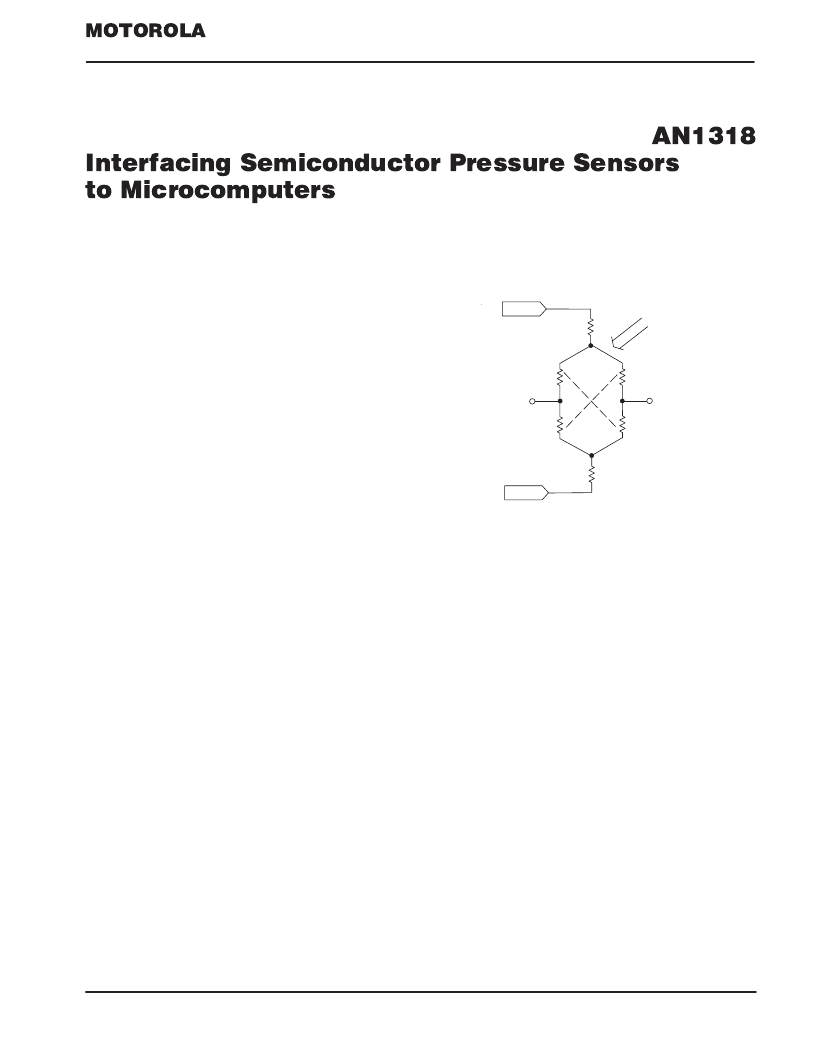
3–269
Motorola Sensor Device Data
For More Information On This Product,
Go to: www.freescale.com
Prepared by: Warren Schultz
Discrete Applications Engineering
INTRODUCTION
The most popular silicon pressure sensors are
piezoresistive bridges that produce a differential output
voltage in response to pressure applied to a thin silicon
diaphragm. Output voltage for these sensors is generally 25
to 50 mV full scale. Interface to microcomputers, therefore,
generally involves gaining up the relatively small output
voltage, performing a differential to single ended conversion,
and scaling the analog signal into a range appropriate for
analog to digital conversion. Alternately, the analog pressure
signal can be converted to a frequency modulated 5 V
waveform or 4–20 mA current loop, either of which is relatively
immune to noise on long interconnect lines.
A variety of circuit techniques that address interface design
are presented. Sensing amplifiers, analog to digital
conversion, frequency modulation and 4–20 mA current loops
are considered.
PRESSURE SENSOR BASICS
The essence of piezoresistive pressure sensors is the
Wheatstone bridge shown in Figure 1. Bridge resistors RP1,
RP2, RV1 and RV2 are arranged on a thin silicon diaphragm
such that when pressure is applied RP1 and RP2 increase in
value while RV1 and RV2 decrease a similar amount.
Pressure on the diaphragm, therefore, unbalances the bridge
and produces a differential output signal. One of the
fundamental properties of this structure is that the differential
output voltage is directly proportional to bias voltage B+. This
characteristic implies that the accuracy of the pressure
measurement depends directly on the tolerance of the bias
supply. It also provides a convenient means for temperature
compensation. The bridge resistors are silicon resistors that
have positive temperature coefficients. Therefore, when they
are placed in series with zero TC temperature compensation
resistors RC1 and RC2 the amount of voltage applied to the
bridge increases with temperature. This increase in voltage
produces an increase in electrical sensitivity which offsets and
compensates for the negative temperature coefficient
associated with piezoresistance.
Since RC1 and RC2 are approximately equal, the output
voltage common mode is very nearly fixed at 1/2 B
+
. In a
typical MPX2100 sensor, the bridge resistors are nominally
425 ohms; RC1 and RC2 are nominally 680 ohms. With these
values and 10 V applied to B
+
, a delta R of 1.8 ohms at full
scale pressure produces 40 mV of differential output voltage.
Figure 1. Sensor Equivalent Circuit
RETURN
B+
RC1
RV1
S+
RP1
RP2
RV2
S–
RC2
PRESSURE
INSTRUMENTATION AMPLIFIER INTERFACES
Instrumentation amplifiers are by far the most common
interface circuits that are used with pressure sensors. An
example of an inexpensive instrumentation amplifier based
interface circuit is shown in Figure 2. It uses an MC33274 quad
operational amplifier and several resistors that are configured
as a classic instrumentation amplifier with one important
exception. In an instrumentation amplifier resistor R3 is
normally returned to ground. Returning R3 to ground sets the
output voltage for zero differential input to 0 V DC. For
microcomputer interface a positive offset voltage on the order
of 0.3 to 0.8 V is generally desired. Therefore, R3 is connected
to pin 14 of U1D which supplies a buffered offset voltage that
is derived from the wiper of R6. This voltage establishes a DC
output for zero differential input. The translation is one to one.
Within the tolerances of the circuit, whatever voltage appears
at the wiper of R6 will also appear as the zero pressure DC
offset voltage at the output.
With R10 at 240 ohms, gain is set for a nominal value of 125.
This provides a 4 V span for 32 mV of full scale sensor output.
Setting the offset voltage to .75 V results in a 0.75 V to 4.75 V
output that is directly compatible with microprocessor A/D
inputs. Over a zero to 50
°
C temperature range, combined
accuracy for an MPX2000 series sensor and this interface is
on the order of
±
10%.
SEMICONDUCTOR APPLICATION NOTE
REV 1
F
Freescale Semiconductor, Inc.
n
.