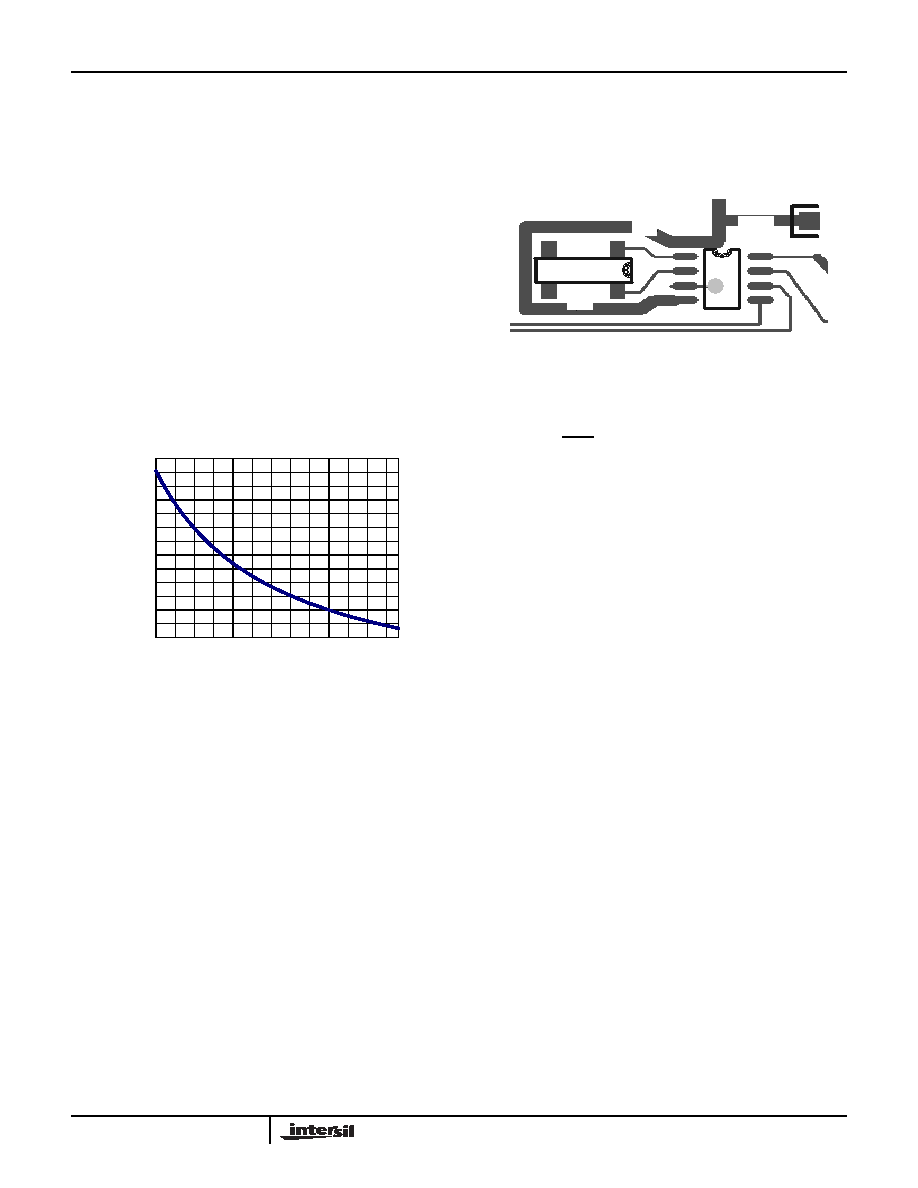
23
FN6731.3
November 24, 2008
the function will just be a matter of implementing software
and performing some calculations. Fairly accurate
temperature compensation can be implemented just by
using the crystal manufacturer’s specifications for the
turnover-temperature T0 and the drift coefficient (β). The
formula for calculating the oscillator adjustment necessary is
Once the temperature curve for a crystal is established, then
the designer should decide at what discrete temperatures
the compensation will change. Since drift is higher at
extreme temperatures, the compensation may not be
needed until the temperature is greater than +20°C from T0.
A sample curve of the ATR setting vs Frequency Adjustment
for the ISL12082 and a typical RTC crystal is given in
Figure
18. This curve may vary with different crystals, so it is
good practice to evaluate a given crystal in an ISL12082
circuit before establishing the adjustment values.
This curve is then used to figure what ATR and DTR settings
are used for compensation. The results would be placed in a
lookup table for the microcontroller to access.
Layout Considerations
The crystal input at X1 has a very high impedance, and
oscillator circuits operating at low frequencies such as
32.768kHz are known to pick up noise very easily if layout
precautions are not followed. Most instances of erratic
clocking or large accuracy errors can be traced to the
susceptibility of the oscillator circuit to interference from
adjacent high speed clock or data lines. Careful layout of the
RTC circuit will avoid noise pickup and insure accurate
clocking.
Figure
19 shows a suggested layout for the ISL12082 device
using a surface mount crystal. Two main precautions should
be followed:
1. Do not run the serial bus lines or any high speed logic
lines in the vicinity of the crystal. These logic level lines
can induce noise in the oscillator circuit to cause
misclocking.
2. Add a ground trace around the crystal with one end
terminated at the chip ground. This will provide
termination for emitted noise in the vicinity of the RTC
device.
In addition, it is a good idea to avoid a ground plane under
the X1 and X2 pins and the crystal, as this will affect the load
capacitance and therefore the oscillator accuracy of the
circuit. If the IRQ1/fOUT pin is used as a clock, it should be
routed away from the RTC device as well. The traces for the
VBAT and VCC pins can be treated as a ground, and should
be routed around the crystal.
Supercapacitor Backup
The ISL12082 device provides a VBAT pin which is used for
a battery backup input. A Supercapacitor can be used as an
alternative to a battery in cases where shorter backup times
are required. Since the battery backup supply current
required by the ISL12082 is extremely low, it is possible to
get months of backup operation using a Supercapacitor.
Typical capacitor values are a few F to 1F or more
depending on the application.
If backup is only needed for a few minutes, then a small
inexpensive electrolytic capacitor can be used. For extended
periods, a low leakage, high capacity Supercapacitor is the
best choice. These devices are available from such vendors
as Panasonic and Murata. The main specifications include
working voltage and leakage current. If the application is for
charging the capacitor from a +5V ±5% supply with a signal
diode, then the voltage on the capacitor can vary from ~4.5V
to slightly over 5.0V. A capacitor with a rated WV of 5.0V
may have a reduced lifetime if the supply voltage is slightly
high. The leakage current should be as small as possible.
For example, a Supercapacitor should be specified with
leakage of well below 1A. A standard electrolytic capacitor
with DC leakage current in the microamps will have a
severely shortened backup time.
Following are some examples with equations to assist with
calculating backup times and required capacitance for the
ISL12082 device. The backup supply current plays a major
part in these equations, and a typical value was chosen for
example purposes. For a robust design, a margin of 30%
should be included to cover supply current and capacitance
tolerances over the results of the calculations. Even more
Adjustment(ppm)
T
0
–
()2
=
β
(EQ. 9)
-400
-30
-20
-10
0
10
20
30
40
50
60
70
80
90
0
5
10 15 20 25 30 35 40 45 50 55 60
ATR SETTING
PP
M
ADJUSTME
N
T
FIGURE 18. ATR SETTING vs OSCILLATOR FREQUENCY
ADJUSTMENT
FIGURE 19. SUGGESTED LAYOUT FOR ISL12082 AND
CRYSTAL
U1
1
Y1
ISL12082