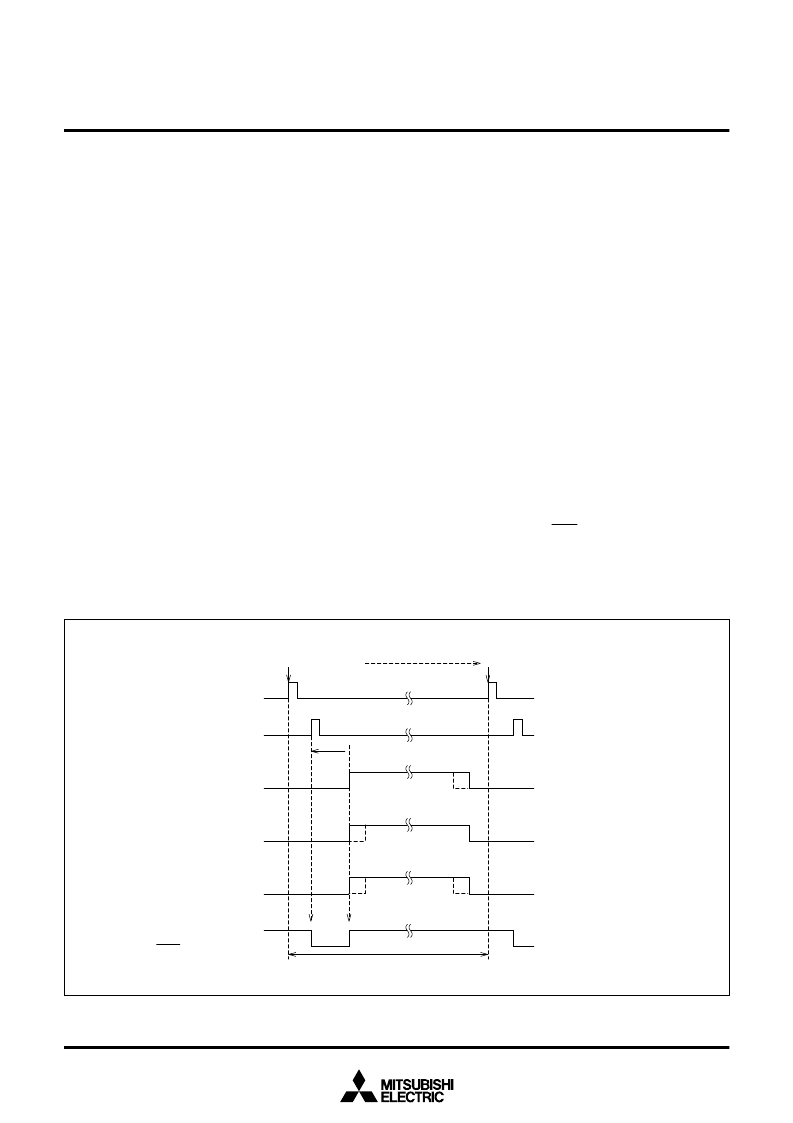
MITSUBISHI
DIGITAL ASSP
M66335FP
FACSIMILE IMAGE DATA PROCESSOR
8
(2) Line cycle and reading sequence
The relationship between the line cycle and the reading sequence of
the M66335 is shown in Fig. 1.
The relationship between the CODEC interface operations and the
reading sequence is shown in Fig. 2 and that between the DMA in-
terface operations and the reading sequence is shown in Fig. 3.
Single-line cycle (1/ACCK):
Defines the processing time per line of the M66335.
The single-line cycle is decided by the line cycle counter value
registers 03 and 04 (PRE_DATA), and the pixel transfer clock.
The pixel transfer clock is 1/16 of SYSCK.
1 line cycle (1/ACCK) [NS]
= line cycle counter value
×
pixel transfer clock cycle [NS]
= (PRE_DATA + 1)
×
pixel transfer clock cycle [NS]
= (PRE_DATA + 1)
×
16/SYSCK [NS]
After loading the PRE_DATA value, the line cycle counter gen-
erates the addresses of the following gate signals while count-
ing down with the pixel transfer clock.
Sensor start pulse (SH):
Image sensor start pulse. The point of the start pulse is decided by
the uniformity correction range (UNIFG) and the value of the reg-
ister 05.
[ST_PL]
The ST_PL value must be set according to the following formu-
las for each image sensor type.
CCD: ST_PL = dummy pixels of the sensor + 2
CIS: ST_PL = 2
Fig. 1 Line cycle and the reading sequence
Line cycle
(ACCK)
Registers 03 and 04
(PRE_DATA)
Sensor start pulse
(SH)
Pulse motor
control
(PTIM)
Register 00 (SENS_W)
Register 11, 12 (OFFSET)
AGC range
(AGCG)
Register 00 (SENS_W)
Register 01 (SOURCE)
Register 00 (SENS_W)
Register 05 (ST_PL)
Original sheet
reading range
1 line cycle
Register 00 (SENS_W)
Uniformity
correction range
(UNIFG)
PRE_DATA loading
ST_PL
Countdown
Relationship with the registers
0
Uniformity correction range (UNIFG):
Defines the range where uniformity correction is performed. This
range corresponds to the width of the sensor (B4 to A4).
For the relationship between the sensor width and the uniformity
correction range, see Table 2.
AGC range (AGCG):
Defines the range where peak value detection is performed. This
range corresponds to the sensor width (B4 to A4).
Auto gain control is performed for the whole width of the sensor
(solid line) in the AGC mode and for the narrower width (dashed
line) than the sensor width in the SCAN mode.
For the relationship between the sensor width and the AGC range,
see Table 2.
Original sheet reading width:
Defines the reading width for original sheets.
For original sheet widths narrower than the sensor width, the read-
ing range (dashed line) is set, using the sensor center as the base
center point. Therefore, the points for the original sheet should be
based on the sensor center.
For the relationship between the sensor width and the original sheet
reading width, see Table 3.
Pulse motor control signal (PTIM):
Generates control signals for the pulse motor for the reading roller.