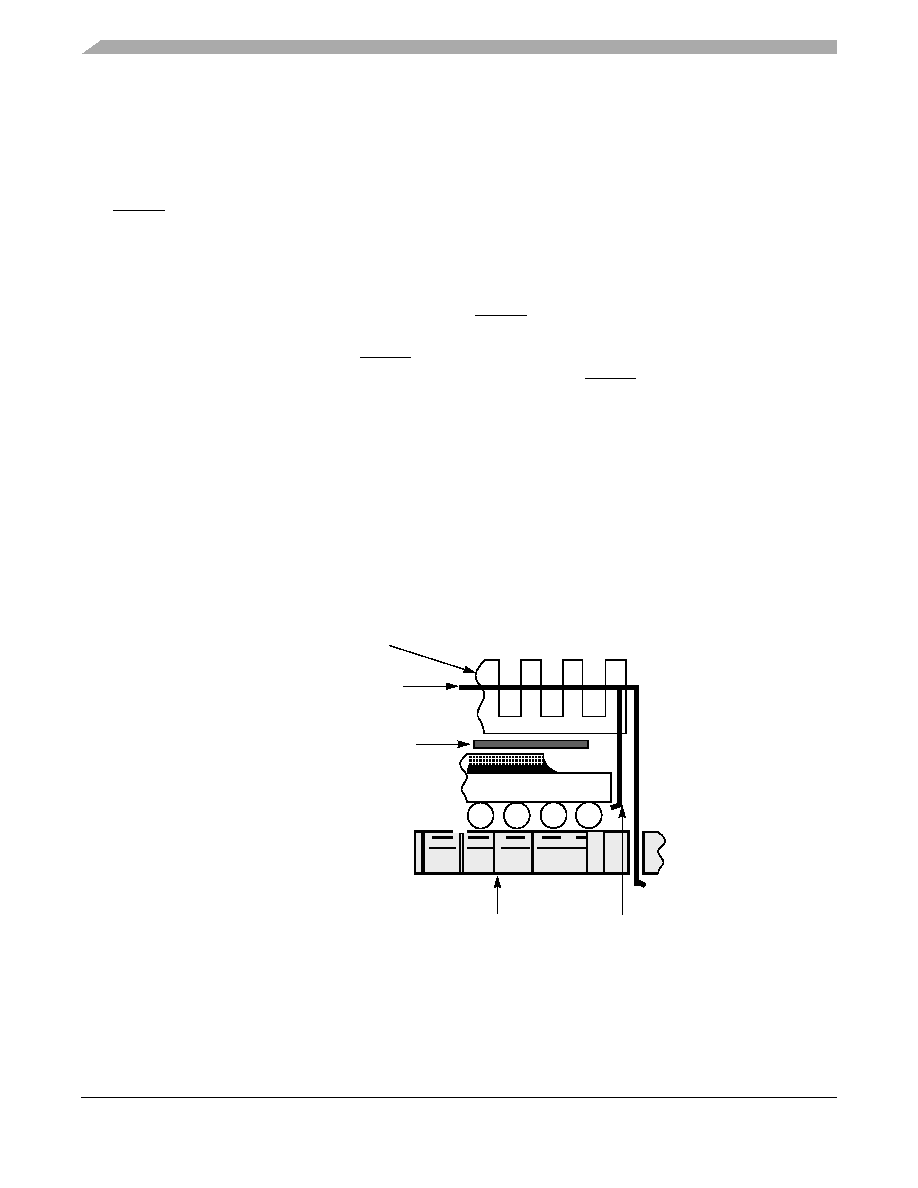
MPC755 RISC Microprocessor Hardware Specifications, Rev. 8
44
Freescale Semiconductor
System Design Information
There is no standardized way to number the COP header shown in
Figure 24; consequently, many different
pin numbers have been observed from emulator vendors. Some are numbered top-to-bottom then
left-to-right, while others use left-to-right then top-to-bottom, while still others number the pins counter
clockwise from pin 1 (as with an IC). Regardless of the numbering, the signal placement recommended in
The QACK signal shown in
Figure 24 is usually connected to the PCI bridge chip in a system and is an
input to the MPC755 informing it that it can go into the quiescent state. Under normal operation this occurs
during a low-power mode selection. In order for COP to work, the MPC755 must see this signal asserted
(pulled down). While shown on the COP header, not all emulator products drive this signal. If the product
does not, a pull-down resistor can be populated to assert this signal. Additionally, some emulator products
implement open-drain type outputs and can only drive QACK asserted; for these tools, a pull-up resistor
can be implemented to ensure this signal is deasserted when it is not being driven by the tool. Note that the
pull-up and pull-down resistors on the QACK signal are mutually exclusive and it is never necessary to
populate both in a system. To preserve correct power-down operation, QACK should be merged via logic
so that it also can be driven by the PCI bridge.
8.8
Thermal Management Information
This section provides thermal management information for air-cooled applications. Proper thermal control
design is primarily dependent on the system-level design—the heat sink, airflow, and thermal interface
material. To reduce the die-junction temperature, heat sinks may be attached to the package by several
methods—adhesive, spring clip to holes in the printed-circuit board or package, and mounting clip and
screw assembly; see
Figure 25. This spring force should not exceed 5.5 pounds (2.5 kg) of force.
Figure 25 describes the package exploded cross-sectional view with several heat sink options.
Figure 25. Package Exploded Cross-Sectional View with Several Heat Sink Options
Adhesive or
Thermal Interface Material
Heat Sink
CBGA Package
Heat Sink
Clip
Printed-Circuit Board
Option