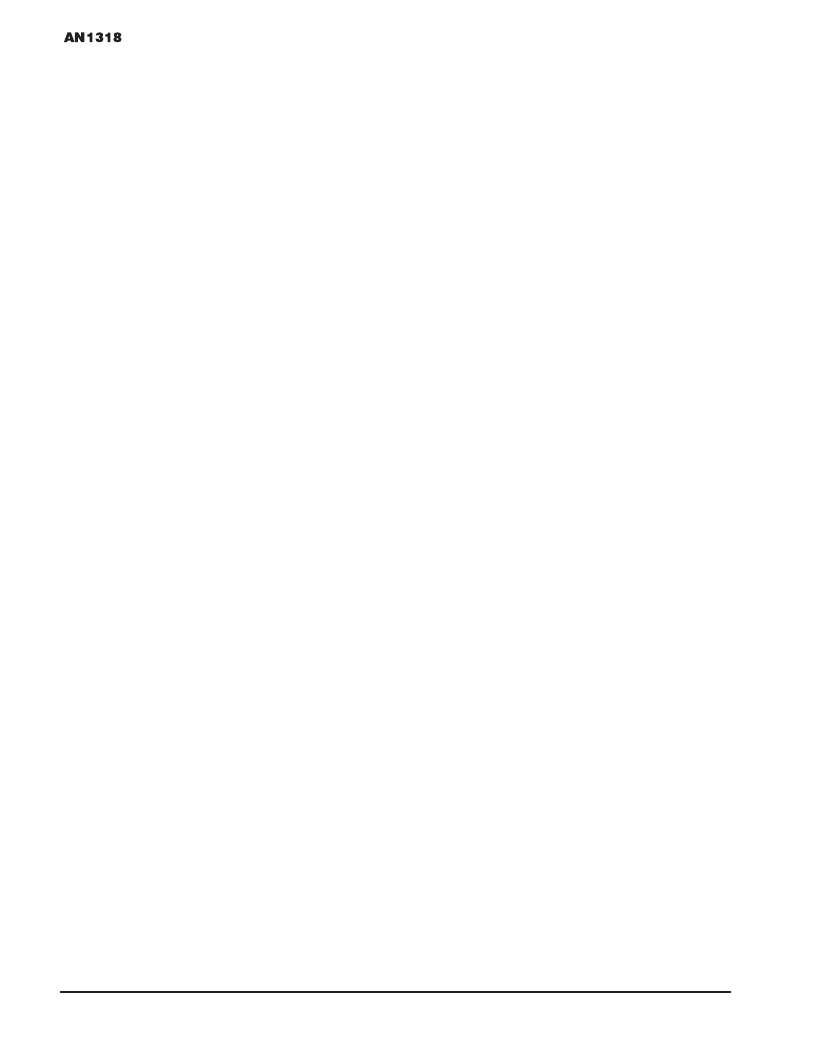
3–278
Motorola Sensor Device Data
For More Information On This Product,
Go to: www.freescale.com
DIRECT INTERFACE
WITH INTEGRATED SENSORS
The simplest interface is achieved with an integrated sensor
and a microcomputer that has an on–chip A/D converter.
Figure 10 shows an LCD pressure gauge that is made with an
MPX5100 integrated sensor and MC68HC05 microcomputer.
Although the total schematic is reasonably complicated, the
interface between the sensor and the micro is a single wire.
The MPX5100 has an internal amplifier that outputs a 0.5 to
4.5 V signal that inputs directly to A/D port PD5 on the HC05.
The software in this system is written such that the
processor assumes zero pressure at power up, reads the
sensor’s output voltage, and stores this value as zero
pressure offset. Full scale span is adjustable with jumpers J1
and J2. For this particular system the software is written such
that with J1 out and J2 in, span is decreased by 1.5%. Similarly
with J1 in and J2 out, span is increased by 1.5%. Given the
±
2.5% full scale spec on the sensor, these jumpers allow
calibration to
±
1% without the use of pots.
MIX AND MATCH
The circuits that have been described so far are intended to
be used as functional blocks. They may be combined in a
variety of ways to meet the particular needs of an application.
For example, the Frequency Output Pressure Sensor in
Figure 8 uses the sensor interface circuit described in Figure
4 to provide an input to the voltage–to–frequency converter.
Alternately, an MPX5100 could be directly connected to pin 4
of the AD654 or the output of Figure 3’s Precision
Instrumentation Amplifier Interface could by substituted in the
same way. Similarly, the Pressure Gauge described in Figure
10 could be constructed with any of the interfaces that have
been described.
CONCLUSION
The circuits that have been shown here are intended to
make interfacing semiconductor pressure sensors to digital
systems easier. They provide cost effective and relatively
simple ways of interfacing sensors to microcomputers. The
seven different circuits contain many tradeoffs that can be
matched to the needs of individual applications. When
considering these tradeoffs it is important to throw software
into the equation. Techniques such as automatic zero
pressure calibration can allow one of the inexpensive analog
interfaces to provide performance that could otherwise only be
obtained with a more costly precision interface.
REFERENCES
1. Baum, Jeff, “Frequency Output Conversion for
MPX2000 Series Pressure Sensors,” Motorola Applica-
tion Note AN1316/D.
2. Lucas, William, “An Evaluation System for Direct Inter-
face of the MPX5100 Pressure Sensor with a Micropro-
cessor,” Motorola Application Note AN1305.
3. Lucas, William, “An Evaluation System for Interfacing the
MPX2000 Series Pressure Sensors to a Microproces-
sor,” Motorola Application Note AN1315.
4. Schultz, Warren, “Compensated Sensor Bar Graph
Pressure Gauge,” Motorola Application Note AN1309.
5. Schultz, Warren, “Interfaced Sensor Evaluation Board,”
Motorola Application Note AN1312.
6. Schultz, Warren, “Sensor Building Block Evaluation
Board,” Motorola Application Note AN1313.
7. Williams, Denise, “A Simple 4–20 mA Pressure Trans-
ducer Evaluation Board,” Motorola Application Note
AN1303.
F
Freescale Semiconductor, Inc.
n
.