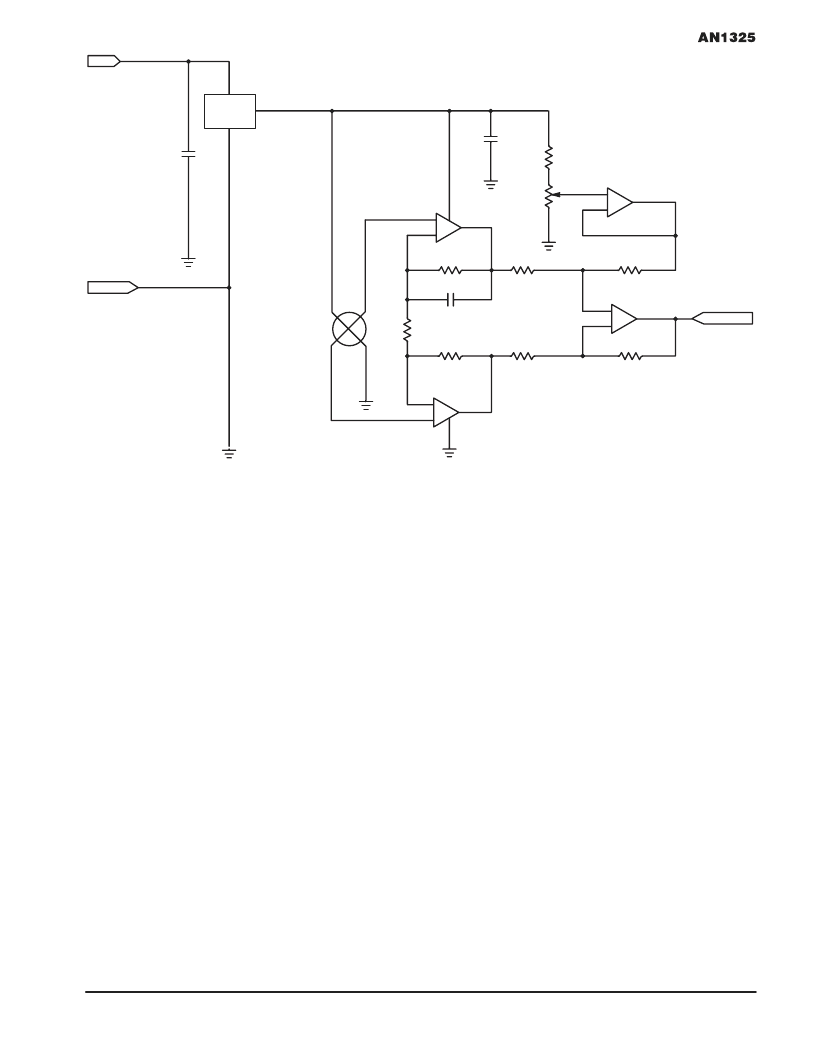
3–285
Motorola Sensor Device Data
For More Information On This Product,
Go to: www.freescale.com
Figure 2. Instrumentation Amplifier Interface
+
–
–
+
XDCR1
MPX2000 SERIES
PRESSURE SENSOR
–
+
–
+
B+
GND
OUTPUT
I
O
G
C1
1
μ
F
U2
MC78L08ACP
3
1
2
1
2
4
3
1
2
3
11
R9
R5
R2
1 k
15 k
U1A
MC33274
1 k
8
9
10
U1C
MC33274
R3 1 k
R4
1 k
U1B
MC33274
R8 15 k
C3
0.001
μ
F
7
4
5
6
C2
0.1
μ
F
R7
7.5 k
ZERO
R6
1 k
12
13
14
U1D
MC33274
* NOTE: FOR MPX2010 R10 = 150 OHMS
R10
240*
To provide the desired DC offset, a slight modification is
made in Figure 2. R3 is connected to pin 14 of U1D, which
supplies a buffered offset voltage that is derived from the wiper
of R6. This voltage establishes a DC output for zero
differential input. The translation is one to one. Whatever
voltage appears at the wiper of R6 will, within component
tolerances, appear as the zero pressure DC offset voltage at
the output.
With R10 at 240
gain is set for a nominal value of 125,
providing a 4 V span for 32 mV of full scale sensor output.
Setting the offset voltage to 0.75 V, results in a 0.75 V to 4.75
V output that is directly compatible with microprocessor A/D
inputs.
This circuit works reasonably well, but has several notable
limitations when made with discrete components. First, it has
a relatively large number of resistors that have to be well
matched. Failure to match these resistors degrades common
mode rejection and initial tolerance on zero pressure offset
voltage. It also has two amplifiers in one gain loop, which
makes stability more of an issue than it is in the following two
alternatives. This circuit also has more of a limitation on zero
pressure offset voltage than the other two. The minimum
output voltage of U1D restricts the minimum zero pressure
offset voltage that can be accommodated, given component
tolerances. The result is a 0.75 V zero pressure offset voltage,
compared to 0.5 V for each of the following two circuits.
SENSOR SPECIFIC AMPLIFIER
The limitations associated with classic instrumentation
amplifiers suggest that alternate approaches to sensor
interface design are worth looking at. One such approach is
shown in Figure 3. It uses one quad op amp and several
resistors to amplify and level shift the sensor’s output.
Most of the amplification is done in U1A, which is configured
as a differential amplifier. It is isolated from the sensor’s minus
output by U1B. The purpose of U1B is to prevent feedback
current that flows through R5 and R6 from flowing into the
sensor. At zero pressure the voltage from pin 2 to pin 4 on the
sensor is zero V. For example, assume that the common
mode voltage is 4.0 V. The zero pressure output voltage at pin
1 of U1A is then 4.0 V, since any other voltage would be
coupled back to pin 2 via R6 and create a non zero bias across
U1A’s differential inputs. This 4.0 V zero pressure DC output
voltage is then level translated to the desired zero pressure
offset voltage by U1C and U1D. To see how the level
translation works, assume that the wiper of R9 is at ground.
With 4.0 V at pin 12, pin 13 is also at 4.0 V. This leaves 4.0 V
across (R3+R9), which total essentially 1 k
. Since no current
flows into pin 13, the same current flows through R4,
producing approximately 4.0 V across R4, as well. Adding the
voltages (4.0 + 4.0) yields 8.0 V at pin 14. Similarly 4.0 V at
pin 10 implies 4.0 V at pin 9, and the drop across R2 is 8.0 V
– 4.0 = 4.0 V. Again 4.0 V across R2 implies an equal drop
F
Freescale Semiconductor, Inc.
n
.