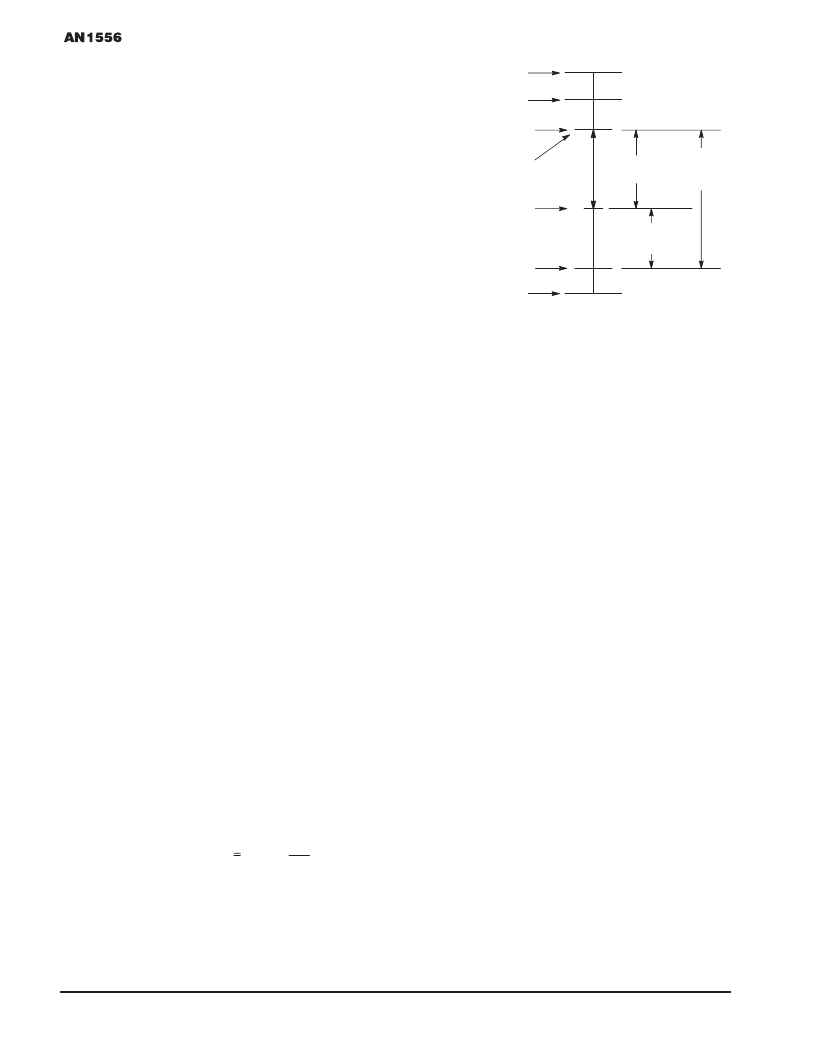
3–350
Motorola Sensor Device Data
For More Information On This Product,
Go to: www.freescale.com
Summarizing (through Step 4), the calculations are based
on a minimum desired resolution. The resolution requirement
determines the number of steps or “pieces” into which the
signal must be broken. This number of steps or “pieces”
multiplied by the number of millivolts per step equals a
minimum voltage range which is defined as the Minimum
Required Span. Finally to ensure that this Minimum Required
Span is achieved over the entire distribution of sensor spans,
the gain is calculated using the worst case smallest sensor
span.
Note:The gain also will have variation due to resistor
tolerances in the amplifier circuit. To ensure that the system
variation due to resistor tolerances is negligible when
compared to other sources of variation, the system should be
designed using resistors with tolerances of 1% or better.
5. Calculate the worst case Maximum Span. The Maximum
Span is the largest possible span and is calculated using
the maximum full–scale sensor voltage span, MaxFSS,
and the Gain. The worst case maximum full–scale sensor
span occurs at the coldest temperature, MinTemp. After
calculating the Maximum Span, the remaining dynamic
range within the A/D’s window or saturation levels of the
amplifier is the smallest number of “bits” (most limiting
case) available for headroom.
Maximum Span =
[Gain]
[MaxFSS]
[1 + TCVFSS
(MinTemp – 25)]
The term [1 + TCVFSS
(MinTemp – 25)] is the temperature
effect on the span.
The Maximum Span calculated from the above equation is
depicted in Figure 4.
6. Calculate the Calculated Headroom. The Calculated
Headroom is a subset of the general term “headroom”
because it reserves “bits” in the A/D’s dynamic range only
for the sources of variation from the sensor’s zero–pres-
sure offset voltage. Headroom, in general, is reserved for
all sources of variation: system components, resistor
tolerances (if significant), and the sensor. However, the
largest part of the “headroom” must be reserved for the
device–to–device variations and temperature effects on
the sensor’s zero–pressure offset voltage. Therefore, the
sources of variation from the other system components
are subtracted immediately from the headroom so that
the focus can be on the sensor–related variations (refer
to Figure 5 and the following equation for the Calculated
Headroom). For these design examples, the supply is a
single, regulated 5 V
±
5% supply (the regulator’s
tolerance is referred to as Vtol). An assumption for a
typical rail–to–rail op–amp’s saturation levels (referred to
as Vlo and Vhi) is 0.2 V above the low supply rail (ground)
and 0.2 V below the high supply rail (5 V). Additionally,
the worst case (smallest) supply voltage is 5 V – 5% or
4.75 V.
Calculated Headroom
·
Vlo– Maximum Span
The preceding equation assumes that the difference
between Vhi and the high supply rail (or high reference of an
A/D) is equal to the difference between Vlo and the low supply
rail (or low reference of an A/D); thus the term (2
Vlo).
5
·
(1–100) – 2
VS’s NOMINAL VALUE
(NOT INCLUDING Vtol)
VS (INCLUDING Vtol) AND
A/D HIGH REFERENCE
HIGH SAT. LEVEL
OF AMPLIFIER
FULL–SCALE
OUTPUT VOLTAGE
ZERO PRESSURE
OFFSET VOLTAGE
LOW SAT. LEVEL
OF AMPLIFIER
GROUND AND A/D
LOW REFERENCE
MAXIMUM
SPAN
CALCULATED
HEADROOM
AMPLIFIER’S
DYNAMIC
RANGE
Figure 5. From Ground to VS, a Section of Voltage Is
Reserved for Each Source of Variation
Step 6 is considered a pivotal step because it transitions the
methodology’s calculations from the performance require-
ments to the headroom requirements. Up to Step 6, the
methodology considered only the span of the sensor to
guarantee a minimum resolution despite device–to–device
variation, component tolerances, and temperature effects.
Upon calculating the Calculated Headroom, the remaining
steps of the methodology that are detailed below consider the
offset variations (due to device–to–device and temperature).
These offset variations are added together to comprise what
is defined as the Required Headroom which is the required
number of “bits” in the A/D’s dynamic range needed to
accommodate the offset variations. This Required Headroom
is then compared to the Calculated Headroom (from the
preceding calculation) to determine if the Calculated Head-
room is sufficient to allow for the offset variations (i.e., the
Calculated Headroom must be greater than or equal to the
Required Headroom). In the case that the Calculated Head-
room is not sufficiently large, relaxing the resolution require-
ment or reducing, if possible, the variation of either offset,
span, component tolerances, or a combination of all three is
required.
7. Calculate the maximum offset drift due to temperature
fluctuations (defined as the Maximum Temperature Effect
on Offset). A conservative approach to this calculation is
to determine the maximum total voltage change of offset
over the application’s entire operating temperature range.
This maximum change of offset is the product of the Gain,
TCVoff, and the application’s entire operating temperature
range (from Maxtemp to MinTemp). Since the tempera-
ture coefficient of offset can be positive or negative, the
offset may increase or decrease with increasing tempera-
ture and, likewise, for decreasing temperature. Though
this step only considers the maximum magnitude of the
change in offset due to temperature, a segment in the
Required Headroom is reserved for both possibilities of a
positive or negative temperature coefficient of offset (see
Figure 6). The sign (positive or negative) of the total offset
change due to temperature is also considered in upcom-
ing steps.
F
Freescale Semiconductor, Inc.
n
.