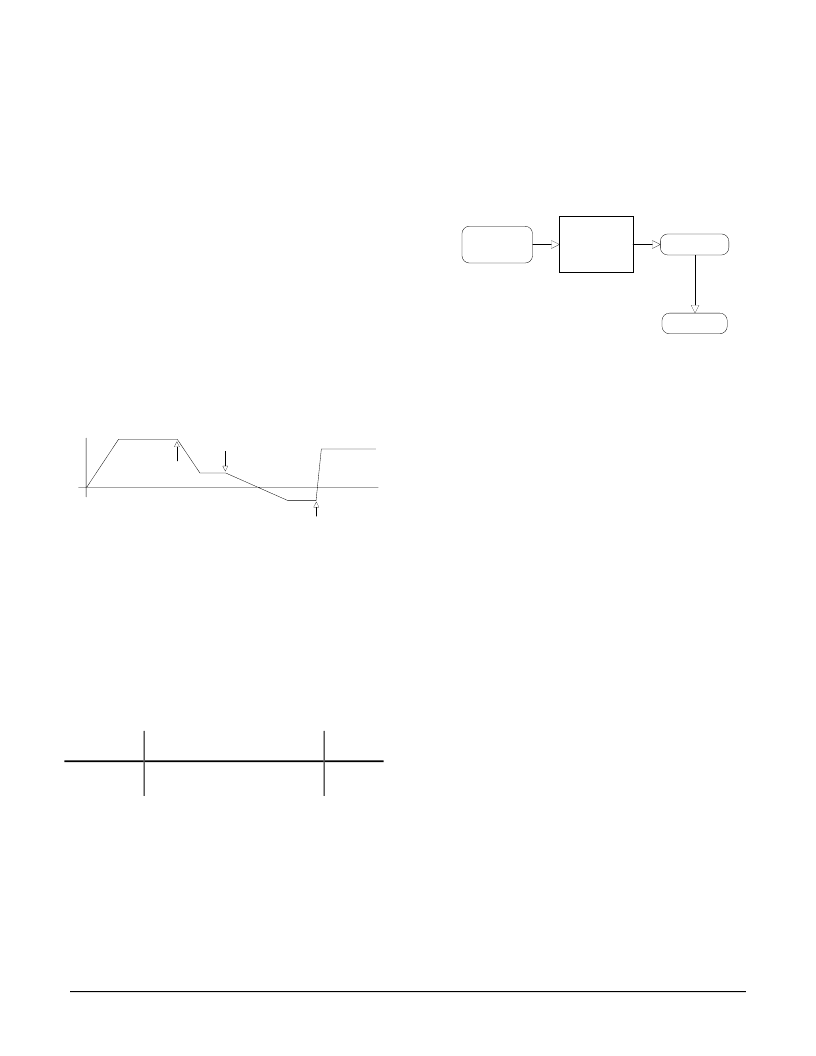
21
multipled by 65,536 and the result is sent to the chipset (-
127,795 dec. or fffe0ccd hex).
In this profile mode the host specifies two parameters, the commanded
acceleration, and the maximumvelocity. The trajectory is executed by
continuously accelerating the axis at the commanded rate until the max.
velocity is reached, or until a new acceleration command is given.
The maximum velocity value must always be positive. Motion
direction is controlled using the acceleration value. Positive
acceleration values result in positive motion, and negative values
result in negative motion.
There are no restrictions on changing the profile parameters on
the fly. Note that the motion is not bounded by position however.
It is the responsibility of the host to generate acceleration and
max. velocity command values which result in safe motion, within
acceptable position limits.
The following figure shows a typical velocity profile using this mode.
Example Velocity Contouring Mode
change
max velocity
change
acceleration
Vel.
Time
change max
velocity and
acceleration
There are no restrictions on switching the profile mode to velocity
contouring while the axis is in motion.
The Starting Velocity can not be changed while the axis is in
motion.
Electronic Gear
The following table summarizes the host specified profile parameters
for the electronic gear profile mode:
Profile
Parameter
Gear Ratio
Representation & Range
Units
signed 32 bits*(1/216 scaling)
-1,073,741,824 to +1,073,741,823
-
*for example to specify a gear ratio of +1.5 to 1 the value
1.5*65,536 is sent to the chipset (98,304). Alternatively to set
the gear ratio as -11.39 to 1 the value -11.39*65,536 is sent (-
746,455 dec. or fff49c29 hex.).
In this profile mode, the host specifies one parameter, the gear ratio.
The target position is generated by applying the specified gear ratio to
the encoder position of the same axis, multiplying by the specified gear
ratio and outputting the corresponding number of mcrosteps.
In this way the output of the mcrostep generator will precisely track the
input encoder position factored by a programmable gear ratio. This can
be useful in many applications where continuous synchronization with
an external mechanismis important.
The following figure shows the arrangement for encoders and motor
drives in a typical electronic gearing application with the MC1241A
Master
Encoder
Motor
Amplifier
MC1241A
Only one of four axes shown
The total number of geared axes supported per chipset is equal to the
number of motor axes. For each motor axes the encoder input for the
same axis is used as the master position command. In addition these
master/slave combinations are fixed, with the encoder for axis 1 driving
the axis 1 mcrostep generator, and the encoder for axis 2 driving the
axis 2 mcrostep generator.
There are no restrictions on changing the gear ratio when the axis
is in motion, although care should be taken to select ratios such
that safe motion is maintained.
There are also no restrictions on changing to this profile mode
while the axes is in motion.
Trajectory Control
Normally each of the above trajectory modes will execute the specified
trajectory, within the specified parameter limts, until the profile
conditions are satisfied. For example for the point-to-point profile modes
this means that the profile will move the axis until the final destination
position has been reached, at which point the axis will have a velocity
of zero.
Halting The Trajectory
In some cases however it is necessary to halt the trajectory manually,
for safety reasons, or simply to achieve a particular desired profile. This
can be accomplished using one of two methods; abrupt stop, or smooth
stop.
Abrupt stops are accomplished using the STOP command. This
command instantaneously stops the trajectory generator by setting the
velocity of the axis to zero. This control mode is typically used during an
emergency stop, when no deceleration phase is desired.
Smooth stops are accomplished using the SMOOTH_STOP command.
This command causes the trajectory to decelerate at a rate equal to the