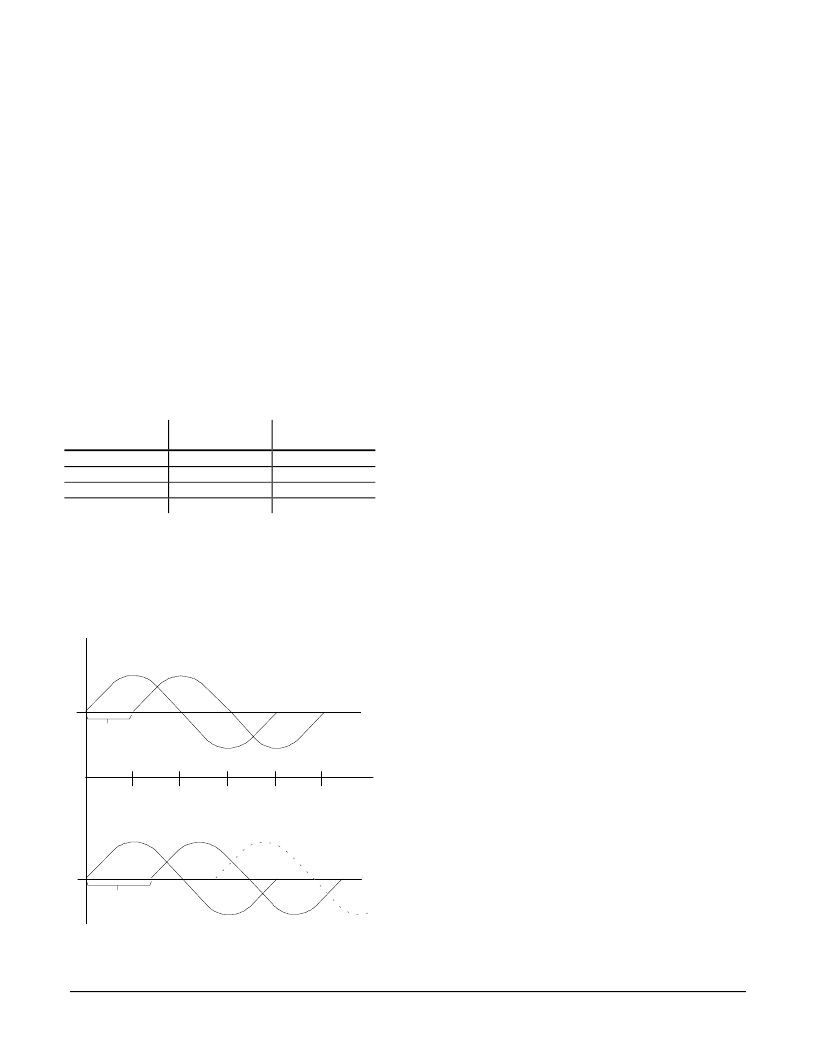
31
as the motor command register. Adjustment of this register by the host
allows different motor power levels during (for example) motion, and at
rest.
Two mcrostepping waveforms are provided, one appropriate for
traditional 2-phase stepper motors with 90 deg. of separation between
phases, and one appropriate for 3-phase stepper motors and AC
Induction motors with 120 deg. separation between phases. For more
information on AC Induction Motor Control see the section entitled AC
Induction Motor Control.
Mcrostepping Waveforms
To specify 2-phase motor waveforms use the command
SET_PHASE_2, and to specify 3-phase motor waveforms use the
command SET_PHASE_3.
Regardless of the waveformselected or the motor output signal format
(PWMor DAC16), 2 output signals per axis will be provided by the
chipset. The following chart shows this.
Waveform
Motor Output Mode
#of Output signals
& Name
2 (A, B)
2 (A, B)
2 (A, B)
2 (A, B)
2-phase
2-phase
3-phase
3-phase
PWM
DAC16
PWM
DAC16
For specific pin assignments of the PWMand DAC16 motor output
signals see the section of this manual entitled 'Pin Descriptions'.
The diagrambelow shows the phase A, B signals for a 2-phase stepper
motor, and the phase A, B signals for a 3-phase stepper motor or AC
Induction motor.
Phase A
Phase B
Phase C
64
128
192
256
120 Deg
Phase A
Phase B
90 Deg
3-Phase Stepper
2-Phase Stepper
320
Microsteps
For 3-phase stepper motors or AC Induction motors, the phase C
waveformmust be constructed externally using the expression C = -
(A+B). Typically this is performed by the motor amplifier itself. See the
following section of this manual entitled "Motor Output" for more
information.
Motor Command Control
The MC1241A provides the ability to set the motor command (power
output) level of the stepper motor. This is often useful to optimze the
motor torque, power consumption, and heat generation of the motor
while it is at rest, or in various states of motion.
The motor output level is controlled by the motor command register.
This register can be set using one of two commands; SET_MTR_CMD
and SET_BUF_MTR_CMD. These commands are identical except that
SET_BUF_MTR_CMD is double buffered, and requires an UPDATE or
a breakpoint to occur before it takes effect. This feature can be used to
advantage when it is desired that the motor power changes be
synchronized with other profile changes such as at the start or the end
of a move.
Changing the power level does not affect the microstepping
output phasing or the frequency of the output waveform, it simply
adjusts the magnitude of the waveform.
AC Induction Motor Control
The MC1241A chipset can be used as the basis of a variable speed 3-
phase AC Induction motor controller. In this mode the chipset is set for
a 3-phase waveform and is operated as if it were a stepper motor. The
position of the motor is not precisely maintained, however the velocity
of the AC Induction motor can typically be controlled to within 10 - 20
percent.
Such a controller can be used for spindles, and other motors where
velocity control, not positioning is required.
When running an AC Induction motor using variable speed control care
should be taken that the output drive signal should never have a
frequency of 0. Even if the motor is not rotating the drive frequency
should have at least some rotational frequency. This is because a
relative difference in the frequency of the drive signals and the motor
rotor (called the slip frequency) is required to avoid magnetic field
saturation at rest, a potentially damaging condition.
Using the MC1241A up to two AC Induction motors can be controlled,
and using the MC1141A one can be controlled. The output drive
configuration is the same as for 3-phase steppers shown in the 'Motor
Output Configuration' section below.
The MC1241A chipset does not provide 'Flux Vector Control' of AC
Induction Motors, only variable speed control. Therefore the
MC1241A should not be used in AC Induction applications
involving precision positioning.